In The Spotlight
Eritrea has issued a tender for the supply of spare parts and equipment for the rehabilitation of gensets and associated substations at its Hirgigo thermal power plant
The country’s Ministry of Energy and Mines, which is behind the tender, has requested bids to be received by 9th September 2025, according to documents published on the African Development Bank (AfDB) website.
The Hirgigo plant, which dates back to the late nineties, has long been one of Eritrea’s most important energy assets, although it was once extensively damaged as a result of conflict in the region around that time.
The power station is located 10 km from the city of Massawa on the Red Sea coast.
The Ministry appears to be utilising funds from the African Development Fund (ADF) — the AfDB’s concessional finance arm — initially allocated for the establishment of the 30 MW Dekemhare Solar PV project.
The Dekemhare project, part of the AfDB's commitment to clean energy on the continent, comprises a solar power plant with a battery energy storage system (BESS), and is currently being built by Chinese contractors, with delivery anticipated as early as the end of the year.
The Eritrean government received financing from ADF toward the cost of Dekemhare “and intends to apply part of the proceeds toward payments under the contract for the procurement of equipment for rehabilitation of substations” the Ministry noted in the documents on the AfDB website.
“The Ministry of Energy and Mines (MoEM) now invites sealed bids from eligible bidders [for the] supply of spare parts for [the] rehabilitation of genset 1 and 2 of Hirgigo power plant and of substations,” it noted.
The AfDB originally approved US$50mn in funding via ADF for the Dekemhare solar project in 2023.
The solar project also includes a 33/66 kV substation and a 66 kV transmission line connected to the existing link between East Asmara and Dekemhare, about 1km from the project site.
Dekemhare itself is located about 40km southeast of the Eritrean capital, Asmara.
At the time of the announcement in 2023, the AfDB said it is expected to contribute to increasing the country’s generation capacity and grid energy to 185 MW and 365 gigawatt-hours/year, respectively.
The bank said the project aims to “guide the transition from over-reliance on fossil fuels for power generation to renewable energy such as solar, wind and geothermal.”
Earlier this year, the AfDB and Eritrea signed a separate agreement for US$19.5mn in grant funding for a Desert to Power Eritrea 12 MW Mini Grid Project.
This is designed to support the rollout of mini-grids that will generate 12 MW of electricity across the regions of Teseney (6MW), Kerekebet (3MW), and Barentu (3MW).
Read more:
Eritrea dam project highlights water sector priorities
Grant funding approved for 12MW Eritrea mini-grid project
ADF approves US5.5mn grant for phase two of flagship Desert-to-Power project
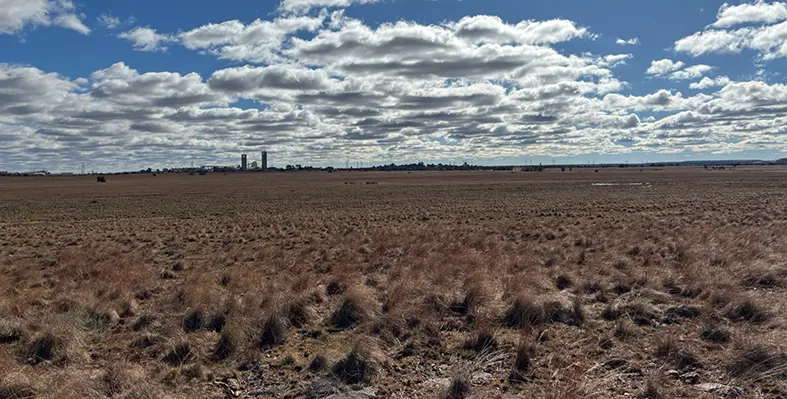
NERSA approves Lyra Energy Trading’s licence, enabling renewable power access for South Africa’s commercial and industrial users. (Image source: Lyra Energy)
Lyra Energy Trading, the trading arm of South Africa-based integrated electricity aggregator Lyra Energy, has received its electricity trading licence from the National Energy Regulator of South Africa (NERSA)
The licence was officially approved on 30 July 2025, following a thorough process that included public hearings and full regulatory compliance.
This development represents a key advancement in Lyra Energy's strategy to deliver clean, affordable power to South Africa’s commercial and industrial markets. With the trading licence in place and access to generation assets secured, Lyra Energy is now positioned as a competitive force in the country’s evolving Wholesale Energy Market. The company aims to offer pricing and contract flexibility to meet the shifting demands of commercial and industrial energy consumers.
Lyra Energy’s trading model includes short-term, standardised power purchase agreements that help mitigate tariff volatility. These agreements also contribute to customers' decarbonisation goals and facilitate the acquisition of green energy credentials.
“We’re proud to be awarded our electricity trading licensed by NERSA, whose role in the transition to the South African Wholesale Energy Market cannot be overstated,” remarked Eben de Vos, head of Lyra Energy. “This award enabling us to use the regulated wheeling framework to buy bulk electricity from Lyra Energy’s generation assets and sell portions thereof to commercial and industrial users.”
Supported by major industry partners
Established in 2024, Lyra Energy is supported by a strategic collaboration led by Scatec and STANLIB Asset Management. Scatec is a leading renewable energy solutions provider, while STANLIB is one of South Africa’s largest asset managers, known for its specialised infrastructure investment team.
Scatec brings to the partnership a broad pipeline of solar, wind, and hybrid projects under development across South Africa and neighbouring regions. The company’s strong track record in delivering and operating energy assets in liberalised markets adds significant operational strength to the initiative.
Meanwhile, the STANLIB Infrastructure Investment team contributes deep infrastructure knowledge and financial mobilisation capabilities, particularly from long-term capital sources such as retirement funds, to accelerate the energy transition.
“Having Lyra Energy as a licensed electricity trader enables the combination of Scatec’s proven development and generation capabilities with STANLIB’s investment leadership to offer a credible utility-scale solution that’s responsive to the energy demands of business.”
Lyra Energy is expected to unveil its first commercial power supply agreement before the end of 2025.
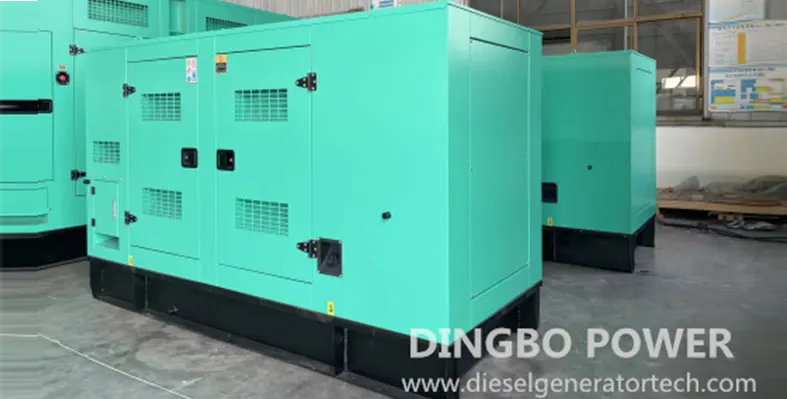
Two 60kVA Yuchai-powered generator sets exported to Tunisia for reliable, quiet backup power in urban locations
Dingbo Power has strengthened its footprint in North Africa with the recent export of two 60kVA silent diesel generator sets to Tunisia
The units, each rated at 48kW/60kVA, were ordered in December 2024 by a Tunisian client seeking reliable power backup solutions for critical applications.
Built for both standby and continuous use, the generators feature integrated base fuel tanks capable of delivering up to eight hours of uninterrupted power. Each unit is equipped with a fuel level sensor connected to a cloud-enabled SmartGen control platform, enabling real-time monitoring and preventing unexpected shutdowns due to fuel depletion.
Noise reduction has also been prioritised in these units, which are housed in soundproof enclosures designed to keep noise levels as low as 75 dB(A) at a distance of seven metres. This makes them well-suited for use in residential neighbourhoods, healthcare facilities, hospitality venues, and office environments—anywhere that demands quiet yet dependable performance.
To support long-term operational efficiency, the order also included essential maintenance accessories such as diesel and oil filters.
These generators combine a robust Yuchai engine with a Shanghai Stamford alternator and advanced control systems, offering a high-performance solution tailored to the needs of global clients. The deployment in Tunisia reflects a growing demand for intelligent, fuel-efficient and low-noise generator technology across Africa.
Dingbo Power continues to specialise in the manufacturing and export of diesel and gas generator sets, delivering customised energy solutions to international markets.
-
-
In the final webinar of its African Review-hosted 2023 campaign, Convergent Group explored its modern, eco-friendly concrete solutions for African projects
Such solutions – delivered to cut maintenance costs by eliminating hazardous silicate products – were showcased by company experts in the form of Jean-Claude Biard, SEO of Convergent Group SA; Mputu Schmidt, former CEO of Convergent Group SA and founder of Bondeko MB (exclusive distributor of Convergent Group in Africa); Carlos Garcia, technical and sales for ADI Group (Spanish distributor for Convergent Group); and Amritpal Singh Sura, external consultant for flooring treatments, former distributor of Convergent products in the Middle East.
“A number of projects we were doing in the Middle East required protection,” remarked Sura. “Longevity of protection requires a system which basically impregnates and becomes a densified surface as opposed to something which is topical and lifts off due to moisture migration. I found that being exposed to Convergent, it was important to stay focused on those systems in the Middle East. Jean-Claude, Mputu and I met several times in Dubai and there was emphasis on providing systems which were affordable and still ending up having a robust, lasting longevity of product. So you are not spending money all the time in order to maintain the finishes which you have already paid for.”
Over the course of the session, the participants guided the audience through the potential of cutting-edge lithium silicate technology for enhancing the protection of concrete surfaces, maximising cost-effectiveness and meeting sustainability targets.
-
In a comprehensive webinar hosted by African Review, a panel of professionals associated with Convergent Group explored new generation lithium silicate technology and why it is emerging as the optimum solution for concrete floor protection.
Robert Daniels, editor of African Review, was joined by Jean-Claude Biard, CEO of Convergent Group; Mputu Schmidt, former CEO of Convergent and founder of Bondeko MB, an exclusive distributor of Convergent; Hicham Sofyani, president of Texol; Carlos Garcia, technical and sales for ADI Group; and Marc Puig, commercial manager of Comace Import.
Each providing a unique angle, the panellists combined to provide a masterclass around concrete treatments and the increasing challenges around them, explaining to attendees how to choose the right formula for their requirements and touching on issues such as why lithium densifiers are better than sodium and potassium densifiers.
Throughout the session, those watching were treated to informative case studies showcasing how Convergent eco-friendly products are increasing abrasion resistance, raising ease of maintenance, and ensuring the highest quality gloss retention.
By the end of the webinar, a majority of attendees (many of which had not had much experience with Convergent) expressed their interest in using the company’s new generation lithium silicate technology with the rest indicating their desire to learn more about Convergent and its products. Watch the webinar, in full, to discover why viewers were convinced and learn more about advanced floor care solutions for your operations.
-
Presenting on an African Review-hosted webinar, Martin Provencher, global industry principal for mining, metals and materials at AVEVA, explored the digital transformation of mining operations and its impact on sustainability.
“Sustainability is becoming a key aspect for mining operations,” remarked Provencher. “If we look at the latest EY research on the top ten business risks and opportunities for mining and metals globally in 2023, ESG remains at the top. Of course, most companies have environmental goals or are expected to reach a net zero emission by 2050, which is a pretty aggressive target. Many of them are targeting 30% reduction by 2030; seven years from now. So there is a lot of action that needs to take place quickly to get there. It is possible to get there, but we need to make sure we are doing this correctly.”
Fast becoming a huge part of ESG initiatives is fleet electrification where particular progress is being made in underground mines. While some countries are certainly more advanced than others here, Provencher noted that 40% of total emissions from the mining industry come from diesel trucks, making EVs a very attractive low-hanging fruit for companies to pursue.
There are, however, a number of challenges associated with bringing in electric vehicles which remains a barrier for introduction. One of the predominant reasons, is the limited range of EVs against diesel counterparts. To mitigate this, Provencher continued, data management is key and ensuring a strong grasp of real-time information coming in will show operators when machinery needs to be charged, allowing them to plan effectively for maximum efficiency on site.
Indeed, this is but a small advantage that digitalisation can bring to the mining industry as it grapples to meet ESG goals while achieving production targets. By getting a better grip of their data and using it to empower tools such as artificial intelligence, advanced analytics and machine learning, companies can achieve tangible benefits such as reduce downtime, enhance worker safety, cut operating costs and, of course, ensure compliance with environmental regulations and targets.
Through the course of the webinar, Provencher outlined this in more detail and explored AVEVA’s suite of cutting-edge software solutions, specifically designed to help mining companies make progress on their digitalisation journey and empower their operations.
Watch the full webinar, completed with detailed case studies and an insightful Q&A session.
-
-
-
Convergent, in association with African Review, has held a detailed webinar exploring the usage and effectiveness of lithium silicates and densifiers over traditional methods of concrete surface management which often struggle to meet the increasing challenges posed by concrete surface management.
Convergent experts including Mputu Schmidt, CEO of Convergent; Carlos Garcia, product manager end-user solutions, construction chemicals, Spain and Portugal for the RD Group; Matteo Mozzarelli, CEO of concrete Solutions Italia; and Jean-Claude Biard, global senior executive for the Convergent Group, presented across the session.
Together, they delved into the latest cost-effective application methods for long lasting finishing of concrete that can help reduce maintenance costs and avoid unexpected repair action. In addition, they examined the advancements in technologies that can sustain increased abrasion resistant stains and ensure gloss retention to the highest quality.
As part of the webinar, the representatives explored case studies including a case in DRC where a medical centre had been constructed with a low-quality concrete floor. The customer was considering completely replacing the floor but instead, Convergent put forward a special treatment with its 244+ Pentra-Sil lithium hardener, densifier and sealer. With this solution, Convergent can increase the hardness of a surface by up to 40% and therefore saved the customer significant recuperation costs over a complete replacement. Convergent were happy to report that the solution was perfect for the facility and the customer was pleased to avoid the extra construction work that would have been required for a complete replacement.
Watch the full webinar, including more information about Convergent’s innovative solutions.
A new €6mn (US$7mn) finance facility has been created to help small businesses in Africa to buy more solar generators
Green Genset Facility (GGF), a not-for-profit empowering small and medium-sized distributors supplying solar generators to the off-grid or weak-grid retail market, will use the grant funding to expand clean energy coverage.
The facility comes via ZE-Gen, a collaborative initiative of the Carbon Trust and Innovate UK, both of which receive backing, directly or indirectly, from UK public funds.
ZE-Gen’s grant funding for GGF is made possible following support for ZE-Gen from IKEA Foundation, a philanthropic organisation.
Maxime Marion, managing director of GGF, said the additional grant funding “enables GGF to power-charge the solar generator market in sub-Saharan Africa.”
Marion added: “For too long small and medium distributors have been priced out of the market by onerous, inaccessible and complex finance facilities, limiting customer choice and restricting competitive market growth and the GGF funding marks a step change in the market.”
Unlike conventional finance, GGF finance is fast and simple, and its iterative approach allows distributors to only buy the stock they are confident they can sell, avoiding costly stockpiling, minimising risk and enabling sustainable growth.
ZE-Gen’s collaboration will allow GGF to ramp up its work breaking down the traditional barriers to financing solar inventory that many small and medium wholesalers face, such as low-ticket sizes, complex due diligence and high transaction costs.
The new funding is part of ZE-Gen’s mission to make renewable energy the affordable go-to source of power in countries where reliable electricity is limited or non-existent and follows a further £10mn (US$13.4mn) in support from the IKEA Foundation earlier this year.
Despite being home to two-thirds of the world’s population, emerging economies currently only account for 15% of global clean energy investment, with homes and businesses facing frequent blackouts that can last for weeks at a time, negatively impacting daily lives, health and business income.
ZE-Gen’s approach tackles market barriers to renewable energy-based alternatives to fossil fuel generators by uniting innovation, finance and skills to drive competitive market growth.
To date, it has catalysed £39.75mn (US$53.4mn) — against a £100mn (US134.4mn) target — and supported more than 30 projects across Nigeria, Ivory Coast, Cote d’Ivoire, South Africa, Malawi and Uganda, as well as Fiji and the Philippines outside Africa.
“Globally, around 1.5 billion people don’t have access to reliable electricity and the potential market for renewable energy generators across sub-Saharan Africa is huge,” said Lily Beadle, ZE-Gen lead at the Carbon Trust.
“The success and failure of any business hinges on being able to access affordable working capital and so ZE-Gen’s involvement with GGF will make a huge difference to the growth of the solar generator market and create new green jobs.”
Read more:
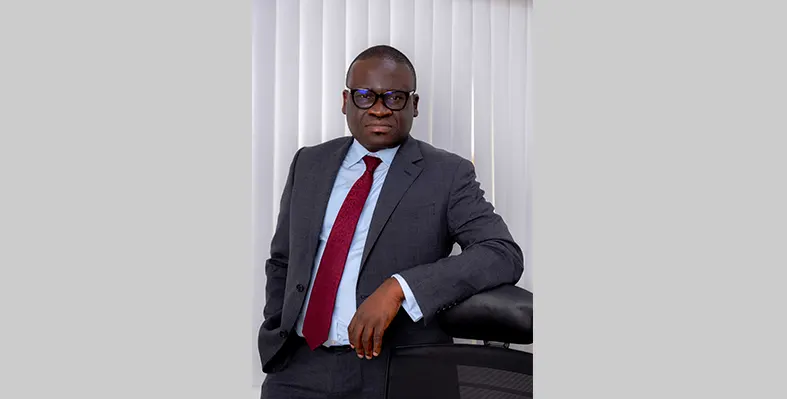
Ajibola Akindele, country president, Nigeria, Schneider Electric West Africa (Image source: Schneider Electric)
Building Management System (BMS): The heartbeat of West Africa’s rapid and intelligent buildings growth. By Ajibola Akindele, country president, Nigeria, Schneider Electric West Africa
West Africa continues to experience phenomenal growth; in fact, in according to research and visualisation mapping tool, Africapolis the region is undergoing one of the fastest urban transitions in the world.
Cities like Lagos, Accra, and Abidjan are driven by population growth, rural-to-urban migration, and economic shifts. By 2050, Africa’s urban population is expected to double, with West Africa becoming a hotspot for mega-agglomerations which are, in essence, sprawling urban zones formed by the fusion of multiple cities.
To meet the above, the building industry needs to mobilise, and quickly. This means everything from high-rise apartments to hospitals, hotels, and office complexes must be built or upgraded to keep pace with the region’s rapid urbanisation.
Intelligent buildings
We also have to build smart. For one, buildings cannot afford to compromise on quality; whilst this might realise short-terms savings, the long-term risks are enormous like comprised safety, inefficiency and system failures.
In West Africa, it’s not uncommon to encounter buildings that appear modern externally but conceal outdated or even unsafe systems within. Many clients, often unknowingly, purchase or install equipment that lacks proper certification or isn’t suited to the building’s operational needs, compromising everything from energy efficiency to fire safety.
This is why at Schneider Electric we cannot emphasise how important it is to integrate standards, intelligent infrastructure at the earliest stages of design. And at the heart of this strategy is Building Management System (BMS).
The tangible benefits
BMS is a powerful solution to sustainably manage urban growth. For example, by optimising HVAC, lighting, and power systems, a BMS platform can reduce energy consumption by up to 30–40%. This is particularly valuable in West African cities, where energy supply can be inconsistent and operational costs high.
Indeed, according to a Frost & Sullivan report. BMS systems are increasingly integrated with renewable energy sources like solar and wind. This synergy enables buildings to dynamically adjust energy usage, reduce grid dependency, and achieve up to 30% operational cost savings.
In retrofitted buildings, BMS offers a non-evasive solution, allowing older structures to be upgraded without the need for full-scale reconstruction.
As an example, in Europe and North America, retrofitting older buildings with BMS has, according to various sources, led to measurable sustainability gains. Buildings undergo significant reduction in energy, improved air quality and occupant comfort and enhanced compliance with building certifications.
Safety and reliability are also key concerns in high-density urban environments. Again, a well-integrated BMS can detect electrical faults, prevent system overloads, and coordinate fire and security responses in real time. This is especially important in sectors like healthcare and hospitality, where service continuity is critical and system failures can lead to costly disruptions or reputational damage.
Beyond operational efficiency, BMS plays a strategic role in supporting sustainable urban development. As mentioned, these systems can integrate with renewable energy sources such as solar panels and microgrids, helping cities reduce their carbon footprint. They also support smart water and waste management, vital capabilities in regions facing water scarcity or infrastructure strain.
Historically, BMS was reserved for high-end commercial buildings, but today, the technology is becoming more accessible and scalable. It’s now being deployed in retail outlets, small businesses, and residential developments, extending its benefits across the rapidly growing West African urban landscape.
Read more:
Schneider Electric powers Nigeria's sustainable manufacturing future
Schneider Electric opens Africa's first innovation hub in Joburg
Transnet SOC Ltd and United Manganese of Kalahari (UMK) have signed a 10-year agreement for transporting manganese by rail from UMK’s Northern Cape mine to export ports
The deal falls under the Manganese Export Capacity Allocation (MECA) 3 framework, through which Transnet allocates rail and port capacity to South African manganese producers. The long-term commitment reflects UMK’s confidence in Transnet’s capability to support access to global markets efficiently.
Transnet group CEO, Michelle Phillips, said, “We are encouraged by the vote of confidence expressed by UMK through their long-term commitment as part of the MECA programme. This agreement is a clear demonstration of our customers’ confidence in the efficiency and reliability of our services. It also bodes well for Transnet’s growth and sustainability, which is underpinned by our ambitious Reinvent for Growth Strategy amid various reform initiatives within the freight logistics sector.”
UMK CEO, Malcolm Curror, emphasised the importance of reliable rail freight, “By enabling the efficient movement of bulk commodities such as manganese, MECA not only positively adds to our national export capability but also to a greater competitive revitalisation of the country’s logistics network.”
He added that this efficiency is vital for sustaining economic growth and encouraging investment across sectors.
Curror also noted, “The MECA agreement holds significant and broader relevance to current national dialogue regarding the mining sector in South Africa.”
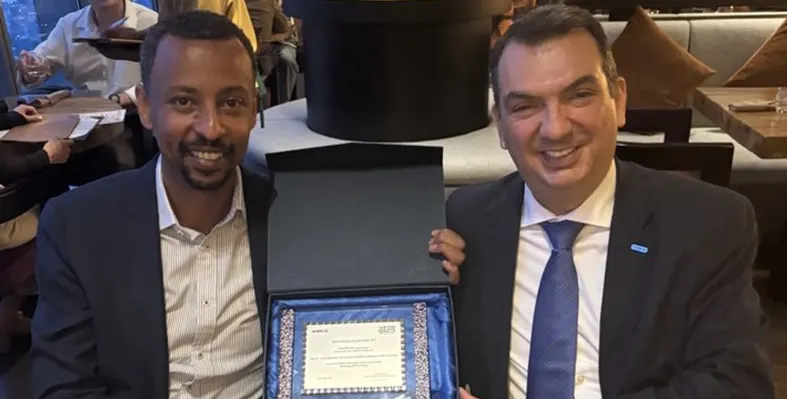
Dr Brook Taye (left), CEO of EIH, pictured with Shahram Falati, IVECO’s business director for Africa & Middle East. (Image source: IVECO)
This year, IVECO and AMCE celebrate 50 years partnership driving Ethiopia’s automotive sector
AMCE (Automotive Manufacturing Company of Ethiopia), a portfolio company of Ethiopian Investment Holdings (EIH), teamed up with global automotive leader IVECO in 1975, a collaboration that has played a defining role in Ethiopia’s transport and industrial development.
Established in 1970 and entering a joint venture with FIAT/IVECO shortly thereafter, AMCE has now assembled and delivered more than 30,000 IVECO commercial vehicles over five decades including the iconic 682N3 trucks, Trakker, IVECO T-Way, Leoncino buses, and specialized trailers built to serve Ethiopia’s growing logistics and public service sectors.
“For 50 years, AMCE and IVECO have worked hand-in-hand to deliver durable, reliable, and locally assembled vehicles that move Ethiopia forward,” said Antonio Caruso, AMCE general manager.
“We are proud of the legacy we’ve built together and look forward to continuing this journey of innovation and partnership.”
Founded in 1970, AMCE operates under a joint venture structure, with 70% ownership by IVECO and 30% by the Ethiopian government through EIH.
The impact of the AMCE and IVECO partnership extends far beyond assembly lines, however.
It has enabled technology and skills transfer across Ethiopia’s industrial ecosystem, spurring the growth of local manufacturers.
The after-sales and maintenance sector has similarly benefited, with technical expertise shared with workshops and service providers from Adama to Bahir Dar.
AMCE’s spare parts dealers throughout the country also allow IVECO customers access to genuine parts.
As Ethiopia continues to prioritise industrialisation and logistics modernisation, IVECO and AMCE remain committed to supporting these national priorities through advanced vehicle solutions, workforce training and local value creation.
“AMCE stands as a model of how joint ventures can deliver long-term economic and social value for Ethiopia,” said Dr Brook Taye, CEO of EIH.
“This partnership has been instrumental in strengthening Ethiopia’s automotive capacity and driving sustainable industrial growth.”
He added: “The next phase of our partnership will focus on addressing the logistics sector constraints in partnership with our portfolio companies and the private sector and introducing a wide range of IVECO’s electric vehicle options to the Ethiopian market.”
Read more:
Daimler Truck vehicle assembly plant in Senegal
A boost for South African automotive manufacturing
IVECO embraces change in product and services renewal
IVECO partners with Al-Imtiyazgroup to expand presence in Libya
Coca-Cola Beverages Africa (CCBA) has invested R365mn (US$20mn) in a new state-of-the-art bottling line at its Midrand plant in South Africa
The high-speed production line is capable of producing 72,000 bottles per hour and marks a South African first, producing Bonaqua Pump Still 750ml and Powerade 500ml packs with a sports bottle cap.
It marks the next step in the global drinks corporation’s ambitions for Africa, where it has pledged to massively hike investment in the coming years.
“By launching this new line, we strengthen our ability to meet growing consumer demand and create shared value across the local value chain, including for our customers and communities,” said Moses Lubisi, manufacturing and technical director at Coca-Cola Beverages South Africa (CCBSA), a company in the CCBA group.
He said the new production line represents a key step in the group’s growth plans across all its African markets in the years ahead, including deepening its commitment to bolster local production and distribution efforts.
“Importantly, this investment reaffirms the Coca-Cola system’s local approach – we produce locally, distribute locally and, where possible, source locally.”
The group is expanding its footprint in other key markets as well.
Last year, Nigeria’s presidency disclosed that the US-based corporation planned to invest US$1bn in the West African state over five years following meetings between President Bola Tinubu and senior executives of the soft drinks company.
In April, CCBA invested US$15mn in a new state-of-the art production line in Lilongwe through its subsidiary Coca-Cola Beverages Malawi Limited (CCBM).
In South Africa, the new production line will also produce Bonaqua Still in 330ml and 500ml packs, further driving the company’s efforts to expand its hydration category.
It will additionally produce the recently launched Powerade Springboks Edition.
To support environmental goals, the new production line features technology to optimise water and energy use.
“At CCBA, our passion for refreshing the continent drives everything we do,” said Sunil Gupta, chief executive officer at CCBA.
“This new production line in South Africa represents a key step in our ambitious growth plans in all our markets on the continent. It enhances our ability to meet consumer needs while reinforcing our commitment to delivering reliability and top-quality beverages across Africa.”
Read more:
Pepsico, Congo Petrol invest in Lubumbashi SEZ
Africa footprint grows as SEW-EURODRIVE builds technical base