In The Spotlight
Power developer Globeleq has signed a share purchase agreement with Norfund, the Norwegian development institution, for the proposed acquisition of a 51% equity stake in Zambia's Lunsemfwa Hydro Power Company (LHPC)
Based in Kabwe, in Zambia’s Central Province, LHPC operates two hydroelectric power plants totaling 56MW and is currently constructing a 20MW solar PV project.
The remaining 49% is owned by Zambian-based infrastructure investment group, Wanda Gorge Investments.
LHPC sells power to the Zambia Electricity Supply Corporation (Zesco) through a power purchase agreement (PPA) and a portfolio of private customers, which include Copperbelt Energy Corporation (CEC) and Jubilee Metals. It also holds a Southern African Power Pool (SAPP) electricity trading license.
Jonathan Hoffman, Globeleq’s CEO, said the agreement marks a pivotal step in the company's Zambian energy market entry.
“We are excited about this opportunity to enter the Zambian market," he said.
"LHPC’s established team, operations and trading capabilities combined with our extensive experience in Africa, create a strong platform to support Zambia’s broader energy objectives and deliver solutions to a range of energy consumers in the region.”
The acquisition also marks the company’s first investment in hydropower in Africa, further enhancing its diversified renewable portfolio which includes solar, wind, battery energy storage (BESS), hybrid solar plus BESS, and geothermal power plants.
Zambia is a priority country for Globeleq’s growth strategy, where the company is leading the development of a 400MW+ greenfield portfolio of solar, wind power, BESS and hybrid projects, including its 54MWp Kafue solar project awarded under the GETFiT Zambia programme.
The completion of the LHPC transaction is expected to be finalised in the latter half of 2025.
Øystein Øyehaug, Norfund investment director, said Globeleq's involvement would unlock LHPC's long-term growth potential.
"With more than 20 years of experience operating in Africa, we are confident that Globeleq is the right fit to lead the LHPC into its next chapter."
Read more:
Globeleq signs up Sungrow for Red Sands project
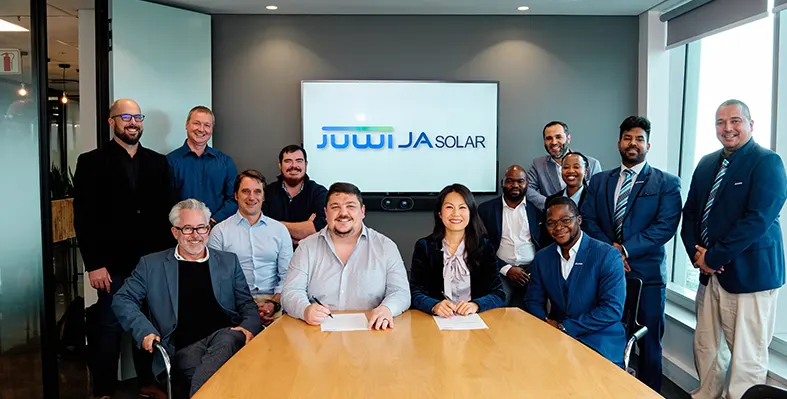
JUWI and JA Solar sign major supply deal for two 220MW utility-scale projects. (Image source: JUWI Renewable Energies)
JUWI Renewable Energies, a global leader in clean energy development, has signed two major solar module supply agreements with JA Solar, a top-tier global manufacturer of high-performance photovoltaic (PV) products
The agreements cover nearly 420,000 solar panels for two large-scale utility projects with a combined capacity of 220MW, supporting some of South Africa’s biggest industrial power users including Glencore, Sasol and Air Liquide.
The projects include the 100MW Sonvanger Solar Plant, being developed for Glencore in partnership with Pele Green Energy, and the 120MW Paarde Valley PV2 Project for Sasol and Air Liquide, delivered with TotalEnergies, Mulilo and Reatile Group. These developments are scheduled to go live by late 2026 and will use enough solar panels to cover more than 160 rugby fields in area.
This agreement is part of JUWI’s broader construction initiative announced earlier this year, representing more than ZAR 6 billion (US$320mn) in new-build solar PV projects. Once completed, these installations will contribute roughly 5% to South Africa’s existing solar PV capacity.
“We’re proud to work with global technology leaders like JA Solar, energy-intensive industries and independent power producers to advance South Africa’s energy transition,” said Richard Doyle, managing director of JUWI Renewable Energies.
“With the country targeting nearly 30 gigawatts of new wind and solar by 2030, and 11 GW of coal capacity scheduled for decommissioning in the near future, we need to ramp up renewable energy deployment faster than ever before if we’re going to keep the lights on. These large-scale projects also bring real carbon savings to the country’s hard-to-abate sectors, while reducing electricity costs for energy users and easing pressure on the grid.”
Aiqing Yang, executive president of JA Solar, stated, “We’re proud to partner with JUWI on these flagship projects, which reflect our shared commitment to advancing clean energy in South Africa. By supplying high-efficiency modules built for performance and reliability, we’re helping to power a more sustainable industrial future.”
Together, the two projects will produce around 672,000 megawatt-hours (MWh) of clean electricity every year. This output is expected to reduce approximately 625,000 tonnes of CO₂ annually, the equivalent of removing more than 130,000 cars from the road, while lowering power costs for industrial users and easing strain on the national grid.
Senegal and Kenya have topped the list of Africa’s leading electricity regulators in a new report highlighting rising standards
The two countries claimed the top spots in the African Development Bank’s (AfDB) 2024 Electricity Regulatory Index (ERI), which evaluates regulatory frameworks across 43 African states.
Uganda, Liberia and Niger round out the top five performers.
Niger registered one of the biggest gains, underlining the strong impact of sustained reforms and political commitment to power sector development, the AfDB noted in a statement.
“The 2024 ERI shows that Africa’s regulators are stepping up,” said Dr Kevin Kariuki, AfDB vice-president for power, energy, climate and green growth.
“We are now seeing stronger institutions delivering real results for utilities and consumers. This shift is critical if we are to achieve Mission 300 and connect 300 million people to electricity by 2030.”
The ERI index evaluates three dimensions: regulatory governance, regulatory substance, and regulatory outcomes (ROI).
The latter category, ROI, which tracks service delivery and utility performance, recorded the most substantial improvements across the continent.
“Now in its seventh edition, the ERI shows strong momentum toward more effective, transparent and impactful regulation, with real-world results beginning to emerge,” the AfDB noted.
The report highlights “standout progress” in Kenya and Senegal in areas such as tariff reform, regulatory outcomes and utility performance.
Crucially, progress is being recorded across the continent with average scores drifting upwards in recent years, and even the lowest-ranked countries seeing imporced scores.
The ROI surged from roughly 0.40 in 2022 to 0.62 in 2024, showing that reforms are delivering tangible service improvements on the ground, the AfDB noted.
Priority areas for enhancing regulatory effectiveness include areas such as strengthening regulatory independence, enhancing accountability mechanisms, promoting transparency and predictability and improving stakeholder participation.
Wale Shonibare, director for energy financial solutions, policy and regulation at the AfDB said the ERI 2024 index tells a hopeful story.
“African countries are not just passing laws — they are implementing them. Regulators are transforming from administrative bodies into strategic institutions with measurable influence. However, challenges related to independence, financing, and enforcement persist.”
Launched in 2018, the ERI is a diagnostic and policy tool used by governments, regulators and development partners to identify gaps, track progress, and prioritise reform efforts.
Read more:
-
-
In the final webinar of its African Review-hosted 2023 campaign, Convergent Group explored its modern, eco-friendly concrete solutions for African projects
Such solutions – delivered to cut maintenance costs by eliminating hazardous silicate products – were showcased by company experts in the form of Jean-Claude Biard, SEO of Convergent Group SA; Mputu Schmidt, former CEO of Convergent Group SA and founder of Bondeko MB (exclusive distributor of Convergent Group in Africa); Carlos Garcia, technical and sales for ADI Group (Spanish distributor for Convergent Group); and Amritpal Singh Sura, external consultant for flooring treatments, former distributor of Convergent products in the Middle East.
“A number of projects we were doing in the Middle East required protection,” remarked Sura. “Longevity of protection requires a system which basically impregnates and becomes a densified surface as opposed to something which is topical and lifts off due to moisture migration. I found that being exposed to Convergent, it was important to stay focused on those systems in the Middle East. Jean-Claude, Mputu and I met several times in Dubai and there was emphasis on providing systems which were affordable and still ending up having a robust, lasting longevity of product. So you are not spending money all the time in order to maintain the finishes which you have already paid for.”
Over the course of the session, the participants guided the audience through the potential of cutting-edge lithium silicate technology for enhancing the protection of concrete surfaces, maximising cost-effectiveness and meeting sustainability targets.
-
In a comprehensive webinar hosted by African Review, a panel of professionals associated with Convergent Group explored new generation lithium silicate technology and why it is emerging as the optimum solution for concrete floor protection.
Robert Daniels, editor of African Review, was joined by Jean-Claude Biard, CEO of Convergent Group; Mputu Schmidt, former CEO of Convergent and founder of Bondeko MB, an exclusive distributor of Convergent; Hicham Sofyani, president of Texol; Carlos Garcia, technical and sales for ADI Group; and Marc Puig, commercial manager of Comace Import.
Each providing a unique angle, the panellists combined to provide a masterclass around concrete treatments and the increasing challenges around them, explaining to attendees how to choose the right formula for their requirements and touching on issues such as why lithium densifiers are better than sodium and potassium densifiers.
Throughout the session, those watching were treated to informative case studies showcasing how Convergent eco-friendly products are increasing abrasion resistance, raising ease of maintenance, and ensuring the highest quality gloss retention.
By the end of the webinar, a majority of attendees (many of which had not had much experience with Convergent) expressed their interest in using the company’s new generation lithium silicate technology with the rest indicating their desire to learn more about Convergent and its products. Watch the webinar, in full, to discover why viewers were convinced and learn more about advanced floor care solutions for your operations.
-
Presenting on an African Review-hosted webinar, Martin Provencher, global industry principal for mining, metals and materials at AVEVA, explored the digital transformation of mining operations and its impact on sustainability.
“Sustainability is becoming a key aspect for mining operations,” remarked Provencher. “If we look at the latest EY research on the top ten business risks and opportunities for mining and metals globally in 2023, ESG remains at the top. Of course, most companies have environmental goals or are expected to reach a net zero emission by 2050, which is a pretty aggressive target. Many of them are targeting 30% reduction by 2030; seven years from now. So there is a lot of action that needs to take place quickly to get there. It is possible to get there, but we need to make sure we are doing this correctly.”
Fast becoming a huge part of ESG initiatives is fleet electrification where particular progress is being made in underground mines. While some countries are certainly more advanced than others here, Provencher noted that 40% of total emissions from the mining industry come from diesel trucks, making EVs a very attractive low-hanging fruit for companies to pursue.
There are, however, a number of challenges associated with bringing in electric vehicles which remains a barrier for introduction. One of the predominant reasons, is the limited range of EVs against diesel counterparts. To mitigate this, Provencher continued, data management is key and ensuring a strong grasp of real-time information coming in will show operators when machinery needs to be charged, allowing them to plan effectively for maximum efficiency on site.
Indeed, this is but a small advantage that digitalisation can bring to the mining industry as it grapples to meet ESG goals while achieving production targets. By getting a better grip of their data and using it to empower tools such as artificial intelligence, advanced analytics and machine learning, companies can achieve tangible benefits such as reduce downtime, enhance worker safety, cut operating costs and, of course, ensure compliance with environmental regulations and targets.
Through the course of the webinar, Provencher outlined this in more detail and explored AVEVA’s suite of cutting-edge software solutions, specifically designed to help mining companies make progress on their digitalisation journey and empower their operations.
Watch the full webinar, completed with detailed case studies and an insightful Q&A session.
-
-
-
Convergent, in association with African Review, has held a detailed webinar exploring the usage and effectiveness of lithium silicates and densifiers over traditional methods of concrete surface management which often struggle to meet the increasing challenges posed by concrete surface management.
Convergent experts including Mputu Schmidt, CEO of Convergent; Carlos Garcia, product manager end-user solutions, construction chemicals, Spain and Portugal for the RD Group; Matteo Mozzarelli, CEO of concrete Solutions Italia; and Jean-Claude Biard, global senior executive for the Convergent Group, presented across the session.
Together, they delved into the latest cost-effective application methods for long lasting finishing of concrete that can help reduce maintenance costs and avoid unexpected repair action. In addition, they examined the advancements in technologies that can sustain increased abrasion resistant stains and ensure gloss retention to the highest quality.
As part of the webinar, the representatives explored case studies including a case in DRC where a medical centre had been constructed with a low-quality concrete floor. The customer was considering completely replacing the floor but instead, Convergent put forward a special treatment with its 244+ Pentra-Sil lithium hardener, densifier and sealer. With this solution, Convergent can increase the hardness of a surface by up to 40% and therefore saved the customer significant recuperation costs over a complete replacement. Convergent were happy to report that the solution was perfect for the facility and the customer was pleased to avoid the extra construction work that would have been required for a complete replacement.
Watch the full webinar, including more information about Convergent’s innovative solutions.
Power grids, water systems, and various industrial operations often stretch into isolated regions where regular in-person supervision is not viable. In these cases, remote monitoring offers a practical solution — but only when the equipment is specifically built to endure the surrounding conditions
Gary Bradshaw, director at remote monitoring specialist Omniflex, outlines the technical demands of deploying such systems in harsh and inaccessible locations, and illustrates their use through a project with a major South African electricity utility.
Monitoring infrastructure in remote areas is fraught with challenges. These environments are frequently subject to extreme weather conditions such as high temperatures, humidity, dust, and electrical storms — all of which can compromise the performance and durability of monitoring equipment. Complicating matters further is the lack of readily available maintenance; deploying technicians to these areas involves considerable time, effort, and cost.
Another major hurdle is the absence of consistent power supply. With no mains electricity, these monitoring systems are reliant on batteries or, where feasible, solar power. Therefore, efficient energy usage is critical, along with pre-emptive battery replacement to prevent system failure and data loss.
Communication is also an obstacle. Remote locations often lack mobile network coverage, and traditional wired connections are cost-prohibitive to install. In such cases, radio and satellite communication are typically the only viable alternatives.
These issues are compounded by concerns about the longevity of monitoring systems. Many commercially available monitoring products are built with planned obsolescence, requiring full system replacements every few years. For hazardous and difficult-to-access sites, this poses both financial and safety concerns.
“For installations in remote and dangerous locations, this is not practical as sending engineers out to regularly replace equipment presents all the same challenges as in-person monitoring and equipment maintenance in terms of cost and risk. For these systems, remote monitoring equipment should ideally maintain full serviceability and compatibility for decades to minimise the need to dispatch engineers and technicians.”
Eskom’s remote monitoring evolution
In the early 1990s, South Africa’s electricity supplier Eskom faced operational difficulties in overseeing its remote assets, particularly 11kV and 22kV distribution lines that passed through isolated rural terrain. Frequent storms brought lightning strikes and fallen branches, which often triggered the auto-reclosers and sectionalisers, disrupting supply.
Restoring these services meant engineers had to navigate long distances — often at night and in hazardous conditions — just to diagnose and manually reset equipment. The problem was exacerbated by poor telecom infrastructure in those regions, causing delays in reporting and response.
To address this, Eskom partnered with Omniflex to implement a remote monitoring system capable of continuous, centralised supervision. The solution involved deploying Maxiflex remote terminal units (RTUs), mounted on power line poles and equipped to operate independently in the field.
“Maxiflex is a modular product that can be configured to suit a wide range of applications and its hot-swappable I/O modules enable maintenance without powering down the system, minimising any associated downtime.”
“The Maxiflex pole-mounted RTUs were mounted directly on power line poles alongside switching devices and interfaced to a central control centre over unlicensed radio bands for secure 24/7 monitoring. This solution allowed operators to receive real-time fault alerts and enabled them to remotely isolate line sections or reset devices without dispatching engineers.”
This was among the earliest deployments of Maxiflex and set the stage for its adoption in various critical infrastructure environments. Since then, the system has been employed in diverse applications globally — from nuclear radiation monitoring in the UK to alarm management and event sequencing in sectors such as oil and gas, petrochemicals, and utilities.
Turkish construction group Summa Turizm Yatirimciligi (Summa) has secured additional funding to help develop various construction projects in Senegal and across sub-Saharan Africa
The company has secured €50mn (US$58mn) in financing from the World Bank’s IFC to develop tourism and urban infrastructure projects across the continent in support of job creation and economic growth.
“We are pleased to have IFC’s support for Summa’s hotel and real estate developments in Senegal and across Africa,” said Selim Bora, chairman of Summa.
“We see this partnership as a foundation for broader collaboration in key sectors such as transportation, sports infrastructure, tourism and energy — areas vital to the region’s sustainable development and economic growth — whereas Summa possesses a deep reservoir of expertise and a strong track record of delivery.”
The loan agreement will help Summa with its working capital and cover capital expenditure needs for construction projects in select countries across Africa.
Established in 1989, Summa’s main focus today is Africa, working across a range of industry sectors and projects including airports, stadiums, hotels, industrial buildings and facilities.
It also works in the construction of motorways, dams, and other infrastructure networks, such as power transmission lines, pipelines, and land reclamation projects.
Current projects include Osvaldo Vieria International Airport in Guinea Bissau and, in the hospitality sector, the new Courtyard Diamniadio hotel in Senegal.
“This investment demonstrates IFC’s commitment to supporting tourism and other urban infrastructure development in African markets,” said Ethiopis Tafara, IFC’s regional vice president for Africa, noting that “these types of investments are essential for driving sustainable economic growth and regional development.”
The combined projects across the region are expected to create more than 2,000 direct and indirect jobs by 2029, while Summa’s operations as a whole will lead to US$225mn in economic value through direct, indirect, and induced effects, the IFC said in a statement.
Read more:
Hilton to triple Africa hotel portfolio
Robust hotels sector growth boosts construction
Liberia inaugurates Arcelormittal concentrator plant
Chinese contractors complete Tanzania's John Magufuli bridge
South Africa’s Condra has received a succession of recent orders for overhead cranes and other lifting equipment that will be deployed across Africa and beyond, as it moves to expand its agent reach across the continent
Among them is an unpack-and-go machine whose shipping containers will become the crane’s gantry, following a deal struck with the company’s agent in Tanzania, Lynx Supply and Services.
The design of this five-ton double-girder crane — a one-off currently under manufacture for mine maintenance — makes use of the two 12-metre delivery containers as gantry supports.
After hoist, crab, girders, end-carriages and other components have been unpacked for assembly, an installation team will position the containers exactly 9.8 metres apart, then bolt rails to their tops to form the gantry.
Lynx, which will carry out the installation and commissioning work, also placed additional orders for wheel blocks, miscellaneous spare parts and a separate 10-ton, 10-metre-span single-girder gantry crane for an unnamed mining house.
Condra’s sub-Saharan agent network also includes Integrated Engineering Services in Zambia, Integrated Engineering Services in the Democratic Republic of Congo (DRC), Namcranes in Namibia and KL Cranes in Botswana.
Management is identifying additional potential agents in Ghana, Mozambique and Kenya, the company said in an update.
Other recent orders received by Condra in sub-Saharan Africa include a 10-ton portal crane for a maintenance application in Ghana.
The design of this crane overcomes floor loading limitations by spreading the machine mass across multiple nylon-treaded wheels at the base of the portal’s supporting legs.
The Ghanaian portal machine is linked to two further crane orders from the same customer, one of them for installation in Saudi Arabia.
Condra noted that it had also received enquiries from Chile and Peru, where the company is reestablishing agency relationships adversely affected by the Coronavirus pandemic.
“Service proximity and availability must be carefully considered alongside purchase price if losses due to downtime are not to negate and even exceed the initial savings of an attractive price,” said a Condra spokesman.
“Condra has long and strong relationships with agents across sub-Saharan Africa to deliver the necessary rapid response time on service calls. Our Johannesburg spares division will deliver parts anywhere in Africa in five days or less, minimising production losses due to crane downtime. In South Africa we deliver in a maximum of 48 hours.”
Read more:
Single crane solution for Ngwadini dam
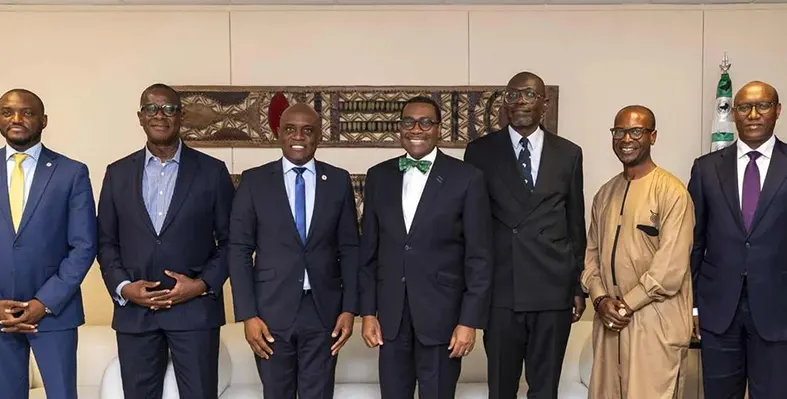
African Development Bank funds feasibility for Rwanda’s US$100mn cable car to improve urban transport access. (Image source: AfDB)
The African Development Bank (AfDB) has approved a US$500,000 grant to fund a feasibility study for Kigali’s proposed aerial urban transit system, set to become sub-Saharan Africa’s first cable car network
The initiative is being spearheaded by Ropeways Transit Rwanda Ltd (RTRL).
The funding comes from the Bank’s Urban and Municipal Development Fund (UMDF) and will support the development of the Kigali Urban Cable Car Project. Valued at US$100mn, the 5.5 km transport solution is designed to alleviate traffic congestion, cut greenhouse gas emissions, and improve access to jobs and essential services for underserved communities.
Hosted by the African Development Bank, the UMDF provides technical assistance and financial support to cities, helping them identify and prepare investment-ready urban projects.
Phase 1 of the project will cover two main routes: from Nyabugogo Taxi Park to the Central Business District, and from the Kigali Convention Center to Kigali Sports City, passing key landmarks such as Amahoro Stadium, BK Arena and Zaria Court.
The feasibility study aims to attract international investment, potentially through platforms such as the Africa Investment Forum (AIF). UMDF has previously supported Rwanda’s Kigali Urban Transport Improvement Project to enhance investor confidence in the transport sector.
Construction is expected to begin in late 2026, with commissioning planned for 2028. Once operational, the system could carry over 50,000 passengers daily on a 15-minute end-to-end journey, fully integrated with Kigali’s broader transport network.
African Development Bank Group president Dr. Akinwumi Adesina said, “This transformative project aligns perfectly with the Bank’s vision for sustainable, green climate-resilient urban mobility infrastructure, and with the Bank’s Ten-Year Strategy, which focuses on urbanisation, and the Alliance for Green Infrastructure in Africa (AGIA), a global partnership initiative driven by the African Development Bank Group, Africa50 and the African Union. By financing Rwanda’s urban cable car system, we are investing in a scalable model of low-carbon, inclusive public transport that cities across Africa can emulate.”
The project also supports Rwanda’s climate targets, as outlined in its Green Taxonomy, E-mobility Strategy and Climate and Nature Finance Strategy, aiming to cut emissions by 38% by 2030 and reach carbon neutrality by 2050.
The cable car project will be implemented under a Public-Private Partnership (PPP), according to Imena Munyampenda, Director General of the Rwanda Transport Development Agency.
The feasibility phase will draw insights from successful cable car systems in cities like La Paz, Bolivia and Singapore, and will incorporate inclusive design principles for disabled access and employment opportunities for women, low-income groups, and youth.
Blended financing model
The project’s US$100mn financing will include grants, concessional loans, blended capital, and technical assistance. The UMDF grant will specifically support assessment of the viability gap. The Rwandan government will partner with the African Development Bank Group and others including IFC, Africa50, TDB, AFC, and private investors under the AGIA to structure blended and commercial finance.
South Africa has entered into a US$1.5bn loan agreement with the World Bank to support the revitalisation of its transport and energy infrastructure and stimulate economic recovery, the National Treasury announced recently
For over ten years, Africa’s most industrialised economy has faced stagnation, hindered by ongoing power outages that have reduced productivity and deteriorating rail systems and port congestion that have impacted key industries like mining and automotive manufacturing.
The government expects the loan to help alleviate transport constraints and bolster energy security, although it has not disclosed which specific projects the World Bank funds will support.
The loan is expected to help manage the country’s rising debt-service burden by offering more favourable conditions than those available in commercial markets, including a three-year grace period.
State-run utilities Eskom and Transnet, responsible for energy and transport respectively, have faced long-standing operational and financial difficulties, contributing to the country’s sluggish growth, which stood at only 0.1% in the first quarter.
The Treasury stated that the interest rate on the 16-year loan from the World Bank is the six-month Secured Overnight Financing Rate plus 1.49%.
This facility is distinct from another US$500mn in funding that the World Bank Group is considering to help mobilise private investment in South Africa’s electricity transmission infrastructure, which needs to be expanded to accommodate more renewable energy projects.
Last month, Finance Minister Enoch Godongwana outlined a budget that includes over 1 trillion rand (US$55.5bn) in investment across sectors including transport, energy, water and sanitation, aimed at driving growth and improving public services.
It aimed for public debt to peak at 77.4% of gross domestic product in the current fiscal year, slowly declining after that.
Initial site work has begun on the construction of a new US$50mn Pepsi bottling plant and a Congo Petrol fuel depot at Kiswishi City Special Economic Zone (SEZ) in Lubumbashi
It represents the first private SEZ in the Democratic Republic of Congo (DRC) and is being developed by Rendeavour, which describes itself as ‘Africa’s new city builder’.
The SEZ project is being supported by American, British, New Zealand and Norwegian investors.
US, British and Congolese government officials took part in a groundbreaking ceremony to mark the start of construction work, alongside executives from PepsiCo (Varun Beverages), Congo Petrol, and Rendeavour.
Preston Mendenhall, group chief operating officer of Rendeavour, said the company’s investment in Kiswishi City SEZ represents “something profound” for the DRC.
“Rather than extracting resources from the landscape, we are literally adding to it, in the form of high-quality infrastructure – power, water, roads, and internet. We are building a mixed-use, mixed-income, inclusive, and environmentally friendly entirely new city for Congolese.”
It is hoped the investments at Kiswishi City SEZ will eventually create thousands of jobs and expand the PepsiCo brand in the DRC’s fast-growing Haut-Katanga Province.
Developed by India's Varun Beverages, Pepsi's largest bottler outside the USA, the facility sits on 15 hectares (37 acres) of land at Kiswishi City SEZ.
Congo Petrol, a distributor and licensee of Kenya's Dalbit Petroleum, will develop a state-of-the-art 8,000 cubic metre petroleum products storage and warehousing facility sitting on seven hectares (17 acres), enhancing its capacity to efficiently serve the growing demand in the region.
Other businesses at Kiswishi City SEZ also include Queen Energy, Zindua Investment, SDG Afrique, Congo Mineral Services and Congolese Analytical Laboratory.
Phase one of Kiswishi's residential estate, Kimia, is 98% sold out.
“Rendeavour and Kiswishi City SEZ — with their American, British, New Zealand and Norwegian shareholders — add tremendous value to our economy by investing in critical infrastructure and well-organised new cities,” said Jean-Marie Kanda, senior advisor to the president of DRC.
“Rendeavour deserves appreciation for the confidence and momentum it has given to the Congolese industrial sector.”
Rendeavour also boasts similar mixed-use cities in Kenya, Nigeria, Ghana and Zambia that have catalysed billions of dollars in foreign and domestic investment, creating thousands of jobs for young Africans.
“Thank you to the investors who believe in the long term,” said Lucy Tamlyn, US Ambassador to the DRC. “Kiswishi City SEZ is very much a long-term investment that requires a lot of faith, confidence, and support.”
Read more:
Emirates Logistics to build new facility in Kenya's Tatu City
Robust hotels sector growth boosts construction