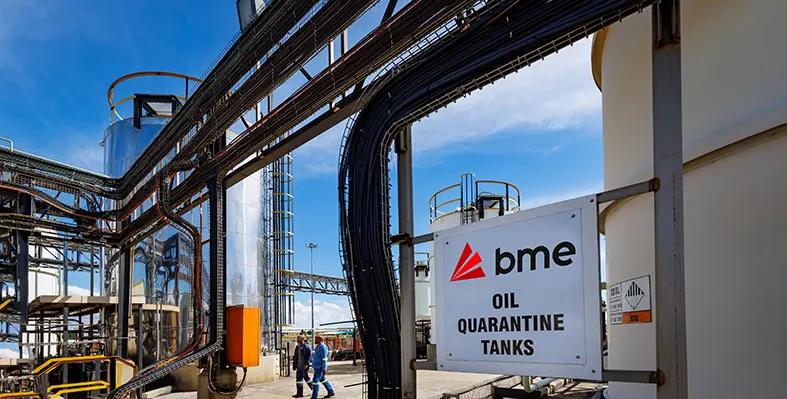
BME's Dryden Innovex manufacturing plant outside of Delmas, Mpumalanga in South Africa (Image source: BME)
BME has outlined its commitment to sustainable mining by incorporating used oil, a hazardous waste, as an ingredient in emulsion explosives
“Through our scientifically rigorous processes, we convert a waste product into a sustainable energy source that can break ground to meet the demands of mining while also promoting environmental sustainability and socio-economic development,” said Sachin Govender, used oil manager at BME.
“Used oil is a major environmental risk. Just one litre can contaminate about a million litres of South Africa’s scarce water resources.”
By consuming up to 20% of all the country’s used oil for the production of emulsions, BME helps to effectively mitigate this risk – while also helping to uplift local communities from where it sources the used oil.
The company utilises used oil as a bioenergy fuel source that is completely consumed in the blasting process — a system it has honed and refined over three decades.
The well-developed and accurate formulations comply with safety regulations and adhere to the company’s ESG goals, said Govender.
He said that while used oil was readily available as it was a waste product, there were various grades, all containing different contaminants and components.
“Therefore, all of the used oil that we collect and process undergoes extensive verification, quality control analysis and validation at our R&D laboratory,” he said.
“The final emulsions that we produce using these technologies are also quality tested to determine their stability, shelf life and efficiency for mining.”
He confirmed that BME was also investigating viable alternatives to traditional used oil.
This would not only enable the company to further pursue greener and more sustainable sourcing, but would also increase its participation in the circular economy.
Read more:
Mining chemicals storage boost for BME
Omnia strengthens global mining offering through rebrand
Blasting solutions for potential acidic sulphate soil