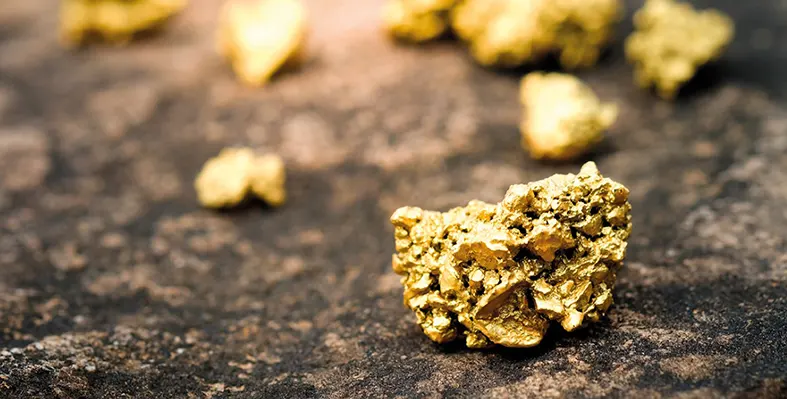
AFC funds Mota-Engil Africa’s gold mining expansion in Côte d’Ivoire, Mali. (Image source: Africa Finance Corporation)
Africa Finance Corporation (AFC), a leading provider of infrastructure solutions across the continent, has extended a €100 million (approx. US$113mn) five-year facility to Mota-Engil Africa (MEA), the regional subsidiary of the global construction powerhouse Mota-Engil Group
This facility will be used to acquire equipment, inventories, and develop site infrastructure for three new gold mining projects in Côte d’Ivoire and Mali.
The funding positions MEA to expand its operations in West Africa’s fast-growing gold sector – a vital contributor to local employment, foreign exchange inflows, and export revenue. The new contracts are expected to significantly enhance the mining landscape in both countries, which remain rich in untapped mineral reserves.
This deal marks a continuation of AFC’s long-standing partnership with Mota-Engil Africa, established in 2016. AFC has previously advised on several key infrastructure projects involving MEA, including Rwanda’s Bugesera International Airport, the US$2bn Kano-Maradi rail line in Nigeria, and Angola’s 1,289 km Lobito Corridor project, where AFC serves as financial adviser to the Lobito Atlantic Railway consortium of MEA, Trafigura, and Vecturis SA.
"This transaction underscores the strength of our decade-long relationship with Mota-Engil Africa and our shared vision to deliver sustainable economic transformation across Africa, commented Samaila Zubairu, president & CEO of Africa Finance Corporation. "Gold continues to be a vital economic driver for many African nations, and through this investment, AFC is helping to unlock long-term value—supporting export earnings, job creation, and broader industrial development of the region."
Manuel Mota, chairman of Mota-Engil Africa, stated, "Today marks a significant milestone for Mota-Engil Africa. We are proud to announce the successful closing of financing for three new mining projects, in partnership with Africa Finance Corporation. This achievement reflects not only the strength of our project portfolio but also the confidence that premier institutions like AFC place in our strategy, our capabilities, and our people."
The investment is part of AFC’s broader effort to grow its involvement in contractor financing – addressing both public and private infrastructure demands. This includes support for Angola’s 186 Metallic Bridges project by Conduril Engenharia S.A., where AFC serves as commercial financier. AFC remains committed to working closely with contractors to bridge Africa’s infrastructure gap while advancing industrialisation, sustainable development, and economic resilience continent-wide.