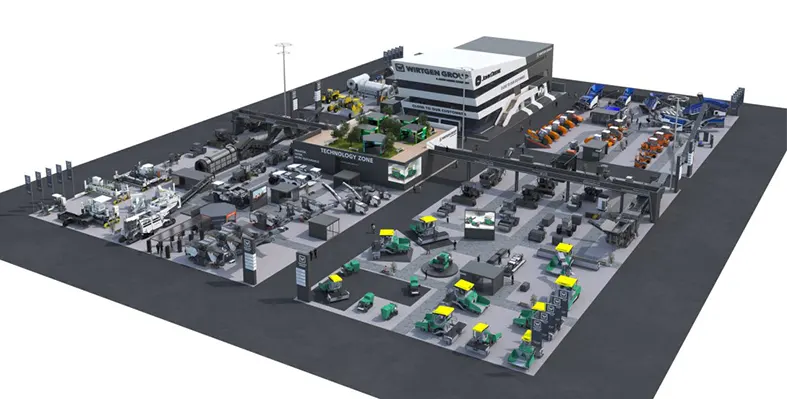
Wirtgen Group at bauma 2025: 100 exhibits, 45 innovations, nine Live Shows, eight Smart Systems on 13,000m² with John Deere. (Image source: Wirtgen Group)
Under the theme ‘Smarter. Safer. More Sustainable,’ the Wirtgen Group, alongside John Deere, is set to showcase an impressive array of cutting-edge solutions at bauma 2025
The joint presence will focus on enhancing efficiency and profitability through advanced construction equipment, innovative technology, and optimised application processes.
Spanning a 13,000 m² booth, the exhibition will feature eight production systems designed for road construction, earthmoving, and materials processing. Visitors can explore nearly 100 machines firsthand and experience, for the first time, nine live demonstrations. The Wirtgen Group has also been shortlisted for the bauma Innovation Award in two categories.
The company will present a range of innovative concrete solutions aimed at tackling key industry challenges, including skilled labor shortages, stringent quality requirements, project documentation, and efficiency improvements.
A Future-ready vision for road construction, earthmoving, and materials processing
As demand for smart, safe, and sustainable solutions grows, the Wirtgen Group is set to introduce state-of-the-art machinery, digital tools, and technologies to optimise construction projects—from planning to documentation and performance analysis.
Technology Zone to feature four world premieres
The Technology Zone will spotlight digital innovations, including the John Deere Operations Center for Construction, a centralised platform for jobsite management. Visitors will also get an exclusive look at the new Wirtgen Group Performance Tracker (WPT) Paving, WPT Compacting, WPT Recycling, and WPT Crushing. These solutions provide real-time performance insights, ensuring enhanced machine utilisation and productivity.
Highlighting smart production systems and award-nominated innovations
The Smart Production System approach integrates the best procedures, digital systems, and machine combinations for optimal efficiency. Attendees can explore cutting-edge machine-trains for applications such as asphalt paving at reduced temperatures, soil stabilisation, and materials processing.
A key highlight is the ‘Production System for a Construction Site with Zero Local Emissions,’ nominated for the bauma Innovation Award in the Climate Protection category. This system, featuring battery-powered milling machines, pavers, and rollers, allows road construction projects to be completed with zero operational emissions.
Another standout innovation is ‘Smart Automation in Roadbuilding,’ a finalist for the bauma Innovation Award in the Digitalization category. This technology automates asphalt removal and paving, ensuring precise results with higher efficiency and reduced resource consumption.
World premieres across all product brands
The Wirtgen Group’s theme ‘Smarter. Safer. More Sustainable.’ will be reflected across numerous world premieres and product innovations. Key highlights include:
-
Wirtgen: Debut of the W 250 XF, the brand’s most powerful large milling machine, and a new generation of wheeled cold recyclers and soil stabilizers.
-
Vögele: Expansion of the Dash 5 series, featuring the new SUPER 1803-5 X-Tier wheeled paver and the MT 3000-5 material feeder.
-
Hamm: Introduction of the HD 10 – HD 12 G-Tier and HD 90 – HD 110 P-Tier tandem rollers, alongside automated compaction solutions like the HC 130i C VA compactor.
-
Kleemann: First-ever PRO line screening plant for natural stone processing.
-
Benninghoven: Presentation of the MULTI JET burner, capable of running on 100% green hydrogen for sustainable asphalt production.
-
John Deere: A lineup of construction equipment, including Compact Track Loaders, Motor Graders, Wheel Loaders, and Dozers.
Live shows: First-of-their-kind demonstrations
For the first time at bauma, the Wirtgen Group will host live demonstrations featuring its latest machines and innovations. Held at booth FS.1011, these engaging sessions will be narrated by industry experts from Wirtgen Group and John Deere, offering deep insights into digitalisation, automation, and process reliability.
With its forward-thinking approach and strong commitment to sustainable innovation, the Wirtgen Group is set to make a major impact at bauma 2025.