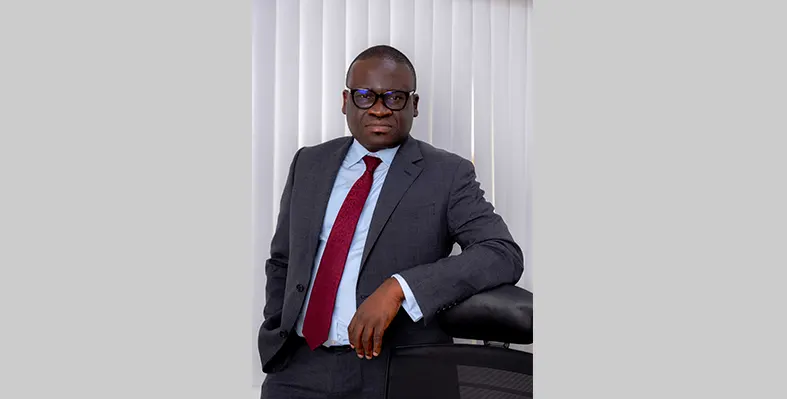
Ajibola Akindele, country president, Nigeria, Schneider Electric West Africa (Image source: Schneider Electric)
Building Management System (BMS): The heartbeat of West Africa’s rapid and intelligent buildings growth. By Ajibola Akindele, country president, Nigeria, Schneider Electric West Africa
West Africa continues to experience phenomenal growth; in fact, in according to research and visualisation mapping tool, Africapolis the region is undergoing one of the fastest urban transitions in the world.
Cities like Lagos, Accra, and Abidjan are driven by population growth, rural-to-urban migration, and economic shifts. By 2050, Africa’s urban population is expected to double, with West Africa becoming a hotspot for mega-agglomerations which are, in essence, sprawling urban zones formed by the fusion of multiple cities.
To meet the above, the building industry needs to mobilise, and quickly. This means everything from high-rise apartments to hospitals, hotels, and office complexes must be built or upgraded to keep pace with the region’s rapid urbanisation.
Intelligent buildings
We also have to build smart. For one, buildings cannot afford to compromise on quality; whilst this might realise short-terms savings, the long-term risks are enormous like comprised safety, inefficiency and system failures.
In West Africa, it’s not uncommon to encounter buildings that appear modern externally but conceal outdated or even unsafe systems within. Many clients, often unknowingly, purchase or install equipment that lacks proper certification or isn’t suited to the building’s operational needs, compromising everything from energy efficiency to fire safety.
This is why at Schneider Electric we cannot emphasise how important it is to integrate standards, intelligent infrastructure at the earliest stages of design. And at the heart of this strategy is Building Management System (BMS).
The tangible benefits
BMS is a powerful solution to sustainably manage urban growth. For example, by optimising HVAC, lighting, and power systems, a BMS platform can reduce energy consumption by up to 30–40%. This is particularly valuable in West African cities, where energy supply can be inconsistent and operational costs high.
Indeed, according to a Frost & Sullivan report. BMS systems are increasingly integrated with renewable energy sources like solar and wind. This synergy enables buildings to dynamically adjust energy usage, reduce grid dependency, and achieve up to 30% operational cost savings.
In retrofitted buildings, BMS offers a non-evasive solution, allowing older structures to be upgraded without the need for full-scale reconstruction.
As an example, in Europe and North America, retrofitting older buildings with BMS has, according to various sources, led to measurable sustainability gains. Buildings undergo significant reduction in energy, improved air quality and occupant comfort and enhanced compliance with building certifications.
Safety and reliability are also key concerns in high-density urban environments. Again, a well-integrated BMS can detect electrical faults, prevent system overloads, and coordinate fire and security responses in real time. This is especially important in sectors like healthcare and hospitality, where service continuity is critical and system failures can lead to costly disruptions or reputational damage.
Beyond operational efficiency, BMS plays a strategic role in supporting sustainable urban development. As mentioned, these systems can integrate with renewable energy sources such as solar panels and microgrids, helping cities reduce their carbon footprint. They also support smart water and waste management, vital capabilities in regions facing water scarcity or infrastructure strain.
Historically, BMS was reserved for high-end commercial buildings, but today, the technology is becoming more accessible and scalable. It’s now being deployed in retail outlets, small businesses, and residential developments, extending its benefits across the rapidly growing West African urban landscape.
Read more:
Schneider Electric powers Nigeria's sustainable manufacturing future
Schneider Electric opens Africa's first innovation hub in Joburg