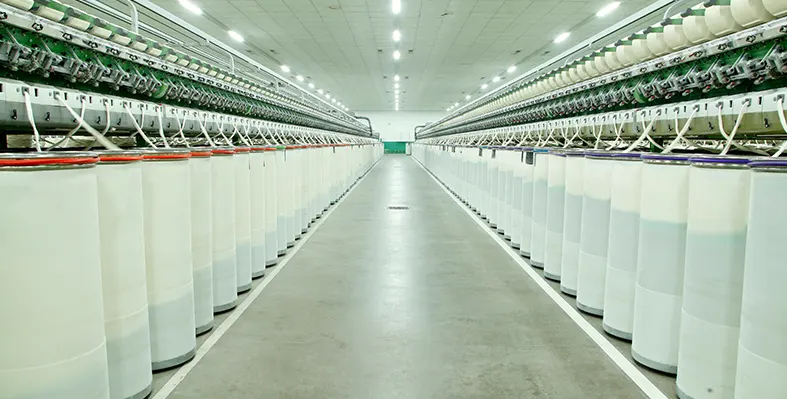
FLS enhances African mill liner capacity through Pretoria-based SSRE acquisition to support mining services
Leading mining technology and service provider FLS has acquired Scott specialised Rubber & Engineering (SSRE), a Pretoria-based company known for producing heavy-duty rubber products used across multiple industries, including mineral processing
The move aligns with FLS’s CORE’26 strategy, which emphasises strategic investments to grow its services portfolio. As a global frontrunner in large grinding mill technology, FLS is focused on expanding mill liner capacity, particularly in regions where supply limitations have affected service delivery.
“This acquisition represents an important milestone in our consumables growth strategy. By introducing mid-sized regional capacity in mill liners, we are enhancing our ability to service mining customers across Africa with greater speed and reliability,” commented Alanas Kraujalis, head of consumables at FLS.
Regional expansion
SSRE’s integration into FLS will enable the local production of rubber and composite mill liners. This change transitions FLS’s mill liner supply chain from an outsourced model to one with dedicated regional capacity.
“The new facility will establish local production of rubber and composite mill liners, shifting our supply model from outsourced to dedicated capacity. This transition will improve control, responsiveness and long-term resilience. Bringing manufacturing closer to our customers enables shorter lead times, more consistent service and strengthened aftermarket support,” Kraujalis added.
The terms of the deal have not been disclosed. The acquisition will not affect FLSmidth’s financial guidance for the full year 2025.
FLS continues to support the global mining sector as a leading original equipment manufacturer (OEM), offering integrated engineering, equipment, and service solutions. Its in-depth knowledge of milling processes ensures customers receive tailored support across the entire milling circuit.