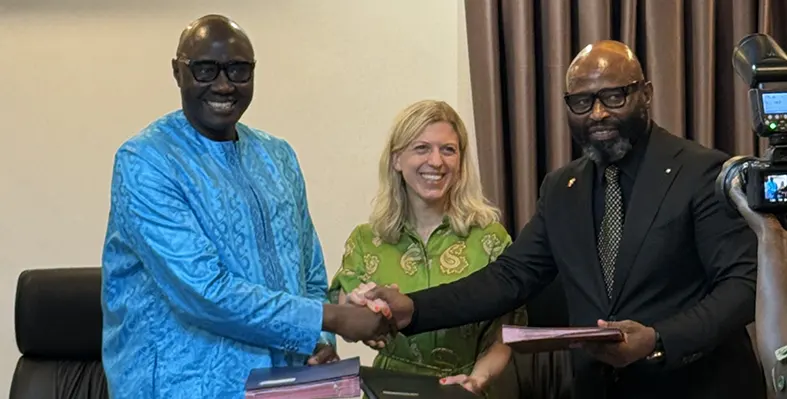
Pictured (left to right): Général Birame Diop, Armed Forces Minister (Defence), with Franziska Cusumano, CEO Mercedes-Benz Special Trucks at Daimler Truck and Cheikh Ibrahima Cisse, President GTS Senegal. (Image source: Daimler Truck)
Pictured (left to right): Général Birame Diop, Armed Forces Minister (Defence), with Franziska Cusumano, CEO Mercedes-Benz Special Trucks at Daimler Truck and Cheikh Ibrahima Cisse, President GTS Senegal. (Image source: Daimler Truck)
COBOD International, in partnership with Technische Universität Braunschweig, has launched the first commercially available multifunctional construction robot, expanding the scope of 3D printing in construction
Unveiled during the grand opening of the Digital Construction Site at TU Braunschweig, the system merges COBOD’s BOD2 3D construction printer with a telescopic vertical extension and robotic arm designed for the Shotcrete 3D Printing Process (SC3DP).
Shotcrete, a concrete-spraying technique typically used in complex structures such as tunnels, retaining walls, and swimming pools, forms the basis of the SC3DP system.
However, the telescopic unit’s versatility allows it to host multiple tool types beyond shotcrete, including sanding equipment, paint spray guns, and insulation tools, transforming the 3D printer into a multifunctional robotic platform.
The system offers a dynamic vertical reach of 3 metres, enabling the robotic arm to operate on printed structures situated up to 3 metres below the X-axis.
This functionality allows users to print, reinforce, and finish complex, double-curved concrete walls with precision and geometric freedom. Reinforcement can either be embedded after concrete placement or applied by spraying around prefabricated reinforcement meshes.
The launch was attended by Helga Kühnhenrich, Head of Research and Innovation in the Construction Industry at Germany’s Federal Institute for Research on Building, Urban Affairs and Spatial Development (BBSR), who highlighted the growing industry focus on automation to cut costs and reduce labour dependence.
According to COBOD, the robotic system can even be equipped with a gripper to automatically install prefabricated elements such as aerated concrete blocks or bricks, features traditionally outside the scope of standard 3D printing setups.
With this, the company aims to redefine what construction robotics can achieve, merging digital precision with functional adaptability.
Henrik Lund-Nielsen, general manager and founder of COBOD International, said, “For years we have had the vision of making multifunctional construction robots on the basis of our 3D construction printers. Seeing the first materialisation of our vision here makes me very proud. With this new technology we offer automation of many more construction processes than just printing of concrete walls. With our new COBOD robotic arm at the end of the telescopic arm there is an endless amount of construction tasks that our printing system can now automate and expedite to the benefit of our global customers.”
Professor Harald Kloft for Structural Design at ITE explained, “Our partnership with COBOD is a decisive step towards the digital construction site of the future. 3D printing enables automated, digitally controlled processes of simple as well as very complex tasks, like the fabrication of reinforced double curved walls. The ability to make complex, individualised, material efficient and low waste construction solutions makes 3D printing ideal for the construction industry, as it brings together economic, environmental and social aspects, such as the reduction of physical stress.”
Rovic’s new factory in Blackheath, Cape Town, with the overhead cranes manufactured by BB Cranes installed and commissioned. (Image source: Condra)
BB Cranes - a subsidiary of South African crane and hoist manufacturer Condra - has installed and commissioned five overhead cranes at a new agricultural machinery factory in Blackheath, Cape Town
Manufactured by BB at the company’s works in Rivergate Industrial Park, the customer, Rovic, which produces agricultural machinery, ordered the cranes as part of a workflow re-engineering to achieve shorter assembly times and improved staff safety.
The changes will help to increase production of the company’s large and small-grain planters.
Rovic manufactures a range of agricultural machinery marketed to customers worldwide under the Syncro brand, with products that include grain planters, mist blowers, spreaders and tillage equipment.
BB manager Jan Nel said the design of the cranes simplifies planter manufacture, allowing simultaneous assembly of individual machines at multiple points.
“We achieved this by fitting 12 independently operated hoists to each of two identical double-girder overhead cranes that we made for Rovic,” Nel said.
“There are six hoists on each crane. They work to assemble multiple planters without having to move the cranes themselves.”
Rovic’s improved assembly sequence replaces the use of forklifts, which in a separate factory used to move components on an as-and-when-required basis to individual planter assembly points serviced by fixed gantries.
In the new assembly sequence, operators position the cranes over planter assembly points arranged in rows across the factory floor.
The hoists work independently to service these points, picking and delivering planter chassis components and up to 53 identical planting units for fitting to each machine.
There are no fixed gantries to obstruct factory movement.
The six hoists fitted to each of the twin double-girder overhead cranes comprise two 3.2-ton crab-mounted units for the chassis components, and four underslung 1-ton hoists fitted two to each girder for the planting units.
All hoists work independently, the girders being spaced at a wider-than-normal 2.5 metres to allow the dedicated chassis hoists to adjust component positions, again without any need to move the cranes.
All the hoists are also fitted with Optidrive variable-speed drives supplied by iTek.
A third BB overhead crane, a 20-tonner, moves completed planters out of the factory for shipping.
In addition, there are two further 2-ton single-girder BB cranes in the Rovic factory, bringing the total to five.
Read more:
Condra expanding agent network after Tanzania crane deal
Cape Town company sets new record with boatbuilding crane
Condra completes second acquisition this year
A high-level roundtable held at the Swedish Embassy during London Climate Action Week has spotlighted the outsized role diesel compact construction machines play in worsening urban air quality, and the urgent need for policy and industry to drive the shift to electric alternatives.
The event brought together city officials, construction leaders and researchers to tackle the overlooked issue of diesel compact machinery, which remains largely exempt from regulations such as London’s Ultra Low Emission Zone (ULEZ) despite emitting significant levels of nitrogen oxides (NOx) and particulate matter (PM). Representatives from Volvo Construction Equipment (Volvo CE), the City of London, and campaign groups joined the call for a rapid transition to zero-emission equipment.
In London alone, approximately 5,000 diesel compact excavators currently in use generate as much NOx and PM as more than 100,000 diesel cars. Yet, because they are not required to meet the same particulate filtration standards as passenger vehicles or larger machines, their impact often goes unaddressed.
With construction now the dominant source of black carbon emissions in London, overtaking cars, the urgency is clear. Globally, only 17% of cities meet WHO air quality guidelines, and air pollution contributed to 8.1 million premature deaths in 2021 alone.
The roundtable also showcased findings from a 12-week trial by Volvo CE, Transport for London (TfL), and FM Conway, which replaced diesel equipment with three electric construction machines. The result: nearly 8kg of harmful NOx and hydrocarbon emissions were avoided, which is the equivalent of a diesel car travelling more than 39,000 miles.
Advocates say electric alternatives offer a win-win: quieter operation, lower vibration, zero tailpipe emissions, and less energy waste, making them ideal for densely populated urban areas. But challenges remain: lack of charging infrastructure, green energy access, regulatory gaps and high upfront costs.
As cities look to scale climate and public health efforts, roundtable participants called for collaborative action to overcome these barriers. Embedding sustainability criteria into public tenders, expanding low emission zones to include all construction machinery, and increasing awareness of compact diesel machines’ impact were highlighted as immediate priorities.
The event closed with a strong message: cleaning up construction emissions is not only technically viable but essential to creating healthier cities. With bold leadership, coordinated policy, and cross-industry collaboration, electric construction machines could play a pivotal role in transforming the urban environment.
Thomas Bitter, Head of the Compact Business Unit at Volvo CE, said, “Cities like London are making great progress to improve air quality. But ignoring construction equipment in low emission policies misses a key health opportunity. Zero-emission solutions exist, but adoption is too slow. We need full value chain collaboration to break down barriers to change and speed up the shift to emission-free construction that is so essential for urban health.”
Turkish construction group Summa Turizm Yatirimciligi (Summa) has secured additional funding to help develop various construction projects in Senegal and across sub-Saharan Africa
The company has secured €50mn (US$58mn) in financing from the World Bank’s IFC to develop tourism and urban infrastructure projects across the continent in support of job creation and economic growth.
“We are pleased to have IFC’s support for Summa’s hotel and real estate developments in Senegal and across Africa,” said Selim Bora, chairman of Summa.
“We see this partnership as a foundation for broader collaboration in key sectors such as transportation, sports infrastructure, tourism and energy — areas vital to the region’s sustainable development and economic growth — whereas Summa possesses a deep reservoir of expertise and a strong track record of delivery.”
The loan agreement will help Summa with its working capital and cover capital expenditure needs for construction projects in select countries across Africa.
Established in 1989, Summa’s main focus today is Africa, working across a range of industry sectors and projects including airports, stadiums, hotels, industrial buildings and facilities.
It also works in the construction of motorways, dams, and other infrastructure networks, such as power transmission lines, pipelines, and land reclamation projects.
Current projects include Osvaldo Vieria International Airport in Guinea Bissau and, in the hospitality sector, the new Courtyard Diamniadio hotel in Senegal.
“This investment demonstrates IFC’s commitment to supporting tourism and other urban infrastructure development in African markets,” said Ethiopis Tafara, IFC’s regional vice president for Africa, noting that “these types of investments are essential for driving sustainable economic growth and regional development.”
The combined projects across the region are expected to create more than 2,000 direct and indirect jobs by 2029, while Summa’s operations as a whole will lead to US$225mn in economic value through direct, indirect, and induced effects, the IFC said in a statement.
Read more:
Hilton to triple Africa hotel portfolio
Robust hotels sector growth boosts construction
Liberia inaugurates Arcelormittal concentrator plant
Chinese contractors complete Tanzania's John Magufuli bridge