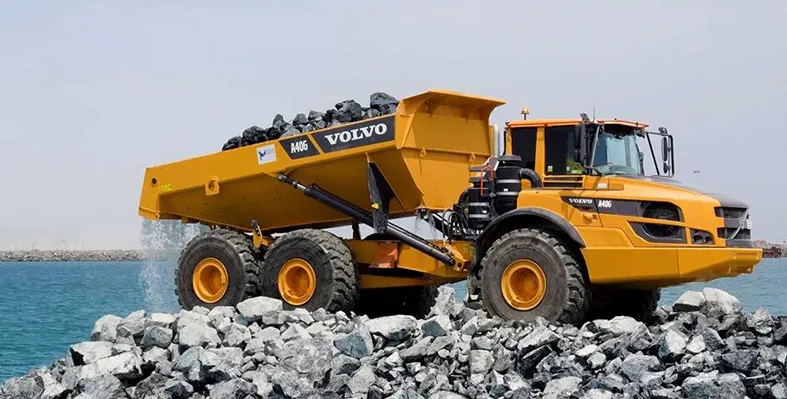
FAMCO supports MAR with Volvo machines, boosting marine and civil construction across Middle East and Africa. (Image source: Volvo CE)
With a robust fleet of Volvo machines provided and supported by Al-Futtaim Auto & Machinery Company (FAMCO), MAR Marine & Building Contracting is taking on technically demanding marine and civil construction projects across the Middle East and Africa, delivering efficiency and minimising downtime
Founded in 2018, MAR Marine & Building Contracting has rapidly established itself as a regional leader in marine and civil infrastructure. Headquartered in both the UAE and Lebanon, with projects spanning multiple countries, MAR has completed more than 200 contracts for over 340 clients, an impressive feat for a relatively new player.
Central to MAR’s success is its focus on quality, timely project delivery and customer satisfaction. The company operates across a wide scope—marine works, steel structures, civil construction, dredging, and sea pipeline installations, serving both public and private clients. Each project poses its own set of challenges, especially in harsh coastal settings where machinery must be both durable and reliable.
Engineering excellence in tough marine conditions
Marine and coastal construction is one of the most complex sectors in the industry, requiring resilience against environmental variables such as saltwater corrosion, fluctuating tides and tight regulatory requirements. To meet these challenges, MAR has invested in more than 40 crawler excavators and articulated haulers from Volvo Construction Equipment.
The Volvo machines have become vital assets in operations such as breakwater construction and sand backfilling. Their corrosion-resistant materials, sealed electrical systems and protected hydraulic components are well suited to marine environments. According to MAR, Volvo’s reputation for robust engineering and performance has been instrumental in their ability to deliver on time.
Partnership rooted in trust
FAMCO, Volvo CE’s long-standing dealer in the UAE, supplies and services MAR’s fleet. This relationship is underpinned by shared values of reliability and service excellence.
“Today we take a moment to thank our trusted partner FAMCO for all their support,” said Marwan Nakhoul, project site engineer at MAR. “In our work, success depends on strong partnerships. FAMCO, together with Volvo Construction Equipment, has always been one of our most trusted partners.”
Nakhoul also pointed to how Volvo’s equipment delivers measurable benefits: “Thanks to the high quality of their machines, we’ve had less downtime and finished our work faster and more efficiently. Our partnership with FAMCO is a big reason for our success.”
Supporting growth across borders
As the demand for marine infrastructure grows across the Middle East and Africa, companies like MAR are playing a key role in driving economic development and coastal resilience. With FAMCO and Volvo CE as dependable partners, MAR is well equipped to expand its footprint—one marine project at a time.