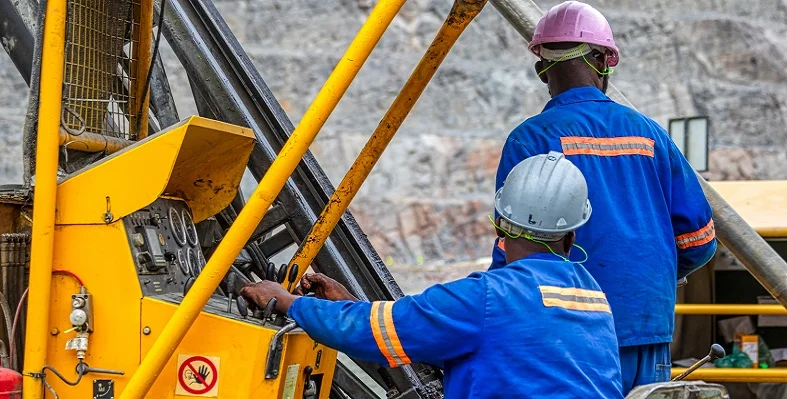
The South African mining sector recorded a decline in year-on-year fatalities as of 14 October. (Image source: Adobe Stock)
Judith Nemadzinga-Tshabalala, South Africa’s Deputy Minister of Mineral and Petroleum Resources, has called for a stronger health and safety culture within the country’s mining industry while speaking at the Mine Health and Safety Summit
“It is to be noted that the implementation of technology alone is not enough,” she remarked. “To achieve zero harm, we must also cultivate and sustain a strong health and safety culture throughout the mining sector. The Health and Safety Culture Transformation Framework developed by the Mine Health and Safety Council provides a solid foundation for this.
“However, the implementation of the framework across the industry remains uneven, and more work is needed to ensure that health and safety is elevated and recognised as a top priority and core value by all stakeholders and every mining operation, from the largest corporations to the smallest operators.”
As of 14 October, the country has recorded that year-on-year fatalities had declined from 38 to 34 deaths (11% in fatalities). Despite the improvement, the Deputy Minister said that even a single death was “one too many” and called for the sector to continue its efforts towards zero harm.
"It is about leadership, accountability and a deep, shared commitment to the well-being of every worker. It requires a shift in mindset, where the health and safety of mineworkers is not seen as an obstacle to productivity, but as a critical component of operational success,” Nemadzinga-Tshabalala continued.
“Many of these incidents are repeats and they can be prevented. Fall of ground accidents remain one of the largest accident categories, and the predominant cause of fatalities followed by general accident and transportation categories, respectively.
“This is regrettable, as it is expected that all mines should have appropriate measures and expertise to enhance the health and safety of mineworkers. So, we urge you to go back to the drawing board and constantly focus on safety performance.”
Constant improvement
The Deputy Minister listed the steps being actioned to reduce incidents within the country’s mining sector including engaging union leaderships; stopping unsafe mines; enforcing and monitoring of health and safety at sites; ensuring safe mining practices are being adopted; and ensuring that all mines collaborate with inspectors and organised labour to have health and safety campaigns to raise awareness.
“South Africa’s mining industry is globally recognised, and our safety record is comparable to some of the leading mining nations,” concluded Nemadzinga-Tshabalala. “However, as demonstrated by countries like Australia and Canada, there are higher benchmarks we can aspire to. We must, therefore, not allow ourselves to become complacent and accept that while the progress we have made is commendable there remains an opportunity for improvement.”