Construction
New generation Volvo excavators stand out
Following the launch of its new generation excavators in Africa and the Middle East, Volvo Construction Equipment (Volvo CE) reveals the specific engineering upgrades that are now delivering enhanced power, durability and fuel efficiency
Earlier this year, the company unveiled a comprehensive renewal of its mid-sized excavator range, encompassing the EC210, EC220, EC230, EC260, EC300 and EC360 models.
To validate their capabilities, the new machines were put to the test in demanding, side-by-side comparisons against both their Volvo predecessors and key competitor models. Operating in real-world conditions, the trials confirmed tangible gains in productivity and fuel economy.
Here are some of the core upgrades that underpin that performance:
1. Upgraded engine power and advanced engine pump technology
At the heart of the larger EC260 to EC360 models is the powerful Volvo D8L engine – the same trusted engine block used in many units from Volvo Trucks and Volvo Buses – delivering proven reliability and performance at a maximum of 1,600 rpm under load.
The EC210-EC230 models, meanwhile, feature a Volvo D5E or D6E engine with a maximum 1,800 rpm under load. The engine performance, combined with state-of-the-art technology MCVs contributes to the machines’ exceptional fuel efficiency, getting more work from every litre of diesel.
For example, the Volvo EC210 demonstrated up to 14% better fuel efficiency over competitors in a similar weight class during the side-by-side tests, while the EC360 recorded up to 21% greater fuel efficiency than the rival machines running at their peak rpm.
2. A new benchmark in structural strength
Moving beyond offering heavy-duty as an option, Volvo CE has engineered the entire new generation as an ‘HD lineup’. The upper frame has been significantly redesigned for increased robustness and strength. This means every machine is built from the ground up for the toughest jobs, such as working in the hard rock quarries of South Africa.
“We made a strategic decision to build the entire range as heavy duty from the start,” said Olle Watz, excavator product manager, Volvo CE region international. “This new standard ensures every excavator is prepared for demanding applications, including continuous work with a hydraulic breaker, providing customers with greater versatility and a more durable asset.”
3. Smarter hydraulics for maximum productivity
A crucial new standard feature on the EC260 to EC360 models specifically is the boom/swing priority function, allowing the operator to intelligently manage hydraulic flow.
“The boom/swing priority is a simple but highly effective feature,” said Watz. “By allowing operators to allocate hydraulic flow where it's needed most, they can significantly cut cycle times in repetitive loading positions common in mining and quarrying. It’s a smart way to boost productivity without any extra cost.”
In the side-by-side tests, the EC360 delivered up to 25% higher productivity than comparable machines from other brands.
4. An operator’s oasis – new ROPS cab and HMI
Recognising that operator performance is also critical, Volvo CE has introduced a completely new human-machine interface (HMI) on the new generation excavators.
To help operators combat fatigue during long, hot shifts, the now ROPS-certified cab features an upgraded air conditioning system, a new clearer display, and a more intuitive layout of controls.
A standard rearview camera and an optional three-point seatbelt enhance site safety, a growing priority on major projects across Africa and the Middle East.
5. Precision and intelligence from Volvo Dig Assist, ready to deploy
To help contractors meet the demands of modern projects, the excavators can be equipped from the factory with the machine control system Volvo Dig Assist. This delivers exceptional accuracy and eliminates the need for time-consuming manual site marking and depth checks.
Key functionalities include 2D for easily setting depth and slope on simpler jobs, In-Field Design for using satellite technology to design and excavate complex shapes with centimetre-level accuracy, and 3D functionality for uploading complex engineering plans for large infrastructure projects. In addition, the On-Board Weighing feature provides real-time data on the bucket’s load, preventing overloading of trucks and ensuring every vehicle is filled to its optimal capacity.
“It was crucial that our customers in the Middle East and Africa have access to the same advanced technology as anywhere else in the world,” said Watz. “The full suite of Dig Assist is available, with system capabilities that are 100% identical to what is offered in Europe. This gives contractors a powerful tool to bid on and execute complex projects with maximum precision.”
A new standard in performance
Taken together, these upgrades represent a significant step forward. By combining a stronger frame, a more efficient powertrain, intelligent hydraulics, and a superior operator environment, the new generation excavators are built to deliver greater uptime, lower running costs, and higher productivity on the region’s most demanding job sites.
Read more:
Machine rebuilds: the African shift to circular construction
Volvo urges electric shift to cut construction equipment emissions
BMS: the heartbeat of Africa’s buildings growth
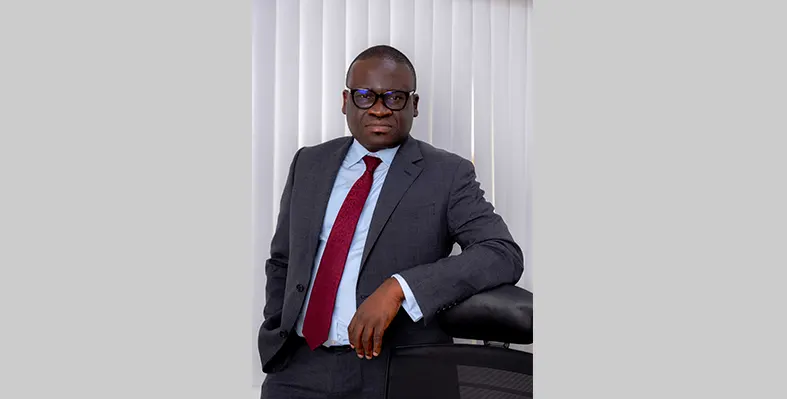
Ajibola Akindele, country president, Nigeria, Schneider Electric West Africa (Image source: Schneider Electric)
Building Management System (BMS): The heartbeat of West Africa’s rapid and intelligent buildings growth. By Ajibola Akindele, country president, Nigeria, Schneider Electric West Africa
West Africa continues to experience phenomenal growth; in fact, in according to research and visualisation mapping tool, Africapolis the region is undergoing one of the fastest urban transitions in the world.
Cities like Lagos, Accra, and Abidjan are driven by population growth, rural-to-urban migration, and economic shifts. By 2050, Africa’s urban population is expected to double, with West Africa becoming a hotspot for mega-agglomerations which are, in essence, sprawling urban zones formed by the fusion of multiple cities.
To meet the above, the building industry needs to mobilise, and quickly. This means everything from high-rise apartments to hospitals, hotels, and office complexes must be built or upgraded to keep pace with the region’s rapid urbanisation.
Intelligent buildings
We also have to build smart. For one, buildings cannot afford to compromise on quality; whilst this might realise short-terms savings, the long-term risks are enormous like comprised safety, inefficiency and system failures.
In West Africa, it’s not uncommon to encounter buildings that appear modern externally but conceal outdated or even unsafe systems within. Many clients, often unknowingly, purchase or install equipment that lacks proper certification or isn’t suited to the building’s operational needs, compromising everything from energy efficiency to fire safety.
This is why at Schneider Electric we cannot emphasise how important it is to integrate standards, intelligent infrastructure at the earliest stages of design. And at the heart of this strategy is Building Management System (BMS).
The tangible benefits
BMS is a powerful solution to sustainably manage urban growth. For example, by optimising HVAC, lighting, and power systems, a BMS platform can reduce energy consumption by up to 30–40%. This is particularly valuable in West African cities, where energy supply can be inconsistent and operational costs high.
Indeed, according to a Frost & Sullivan report. BMS systems are increasingly integrated with renewable energy sources like solar and wind. This synergy enables buildings to dynamically adjust energy usage, reduce grid dependency, and achieve up to 30% operational cost savings.
In retrofitted buildings, BMS offers a non-evasive solution, allowing older structures to be upgraded without the need for full-scale reconstruction.
As an example, in Europe and North America, retrofitting older buildings with BMS has, according to various sources, led to measurable sustainability gains. Buildings undergo significant reduction in energy, improved air quality and occupant comfort and enhanced compliance with building certifications.
Safety and reliability are also key concerns in high-density urban environments. Again, a well-integrated BMS can detect electrical faults, prevent system overloads, and coordinate fire and security responses in real time. This is especially important in sectors like healthcare and hospitality, where service continuity is critical and system failures can lead to costly disruptions or reputational damage.
Beyond operational efficiency, BMS plays a strategic role in supporting sustainable urban development. As mentioned, these systems can integrate with renewable energy sources such as solar panels and microgrids, helping cities reduce their carbon footprint. They also support smart water and waste management, vital capabilities in regions facing water scarcity or infrastructure strain.
Historically, BMS was reserved for high-end commercial buildings, but today, the technology is becoming more accessible and scalable. It’s now being deployed in retail outlets, small businesses, and residential developments, extending its benefits across the rapidly growing West African urban landscape.
Read more:
Schneider Electric powers Nigeria's sustainable manufacturing future
Schneider Electric opens Africa's first innovation hub in Joburg
How will Komatsu empower Africa’s construction workforce?
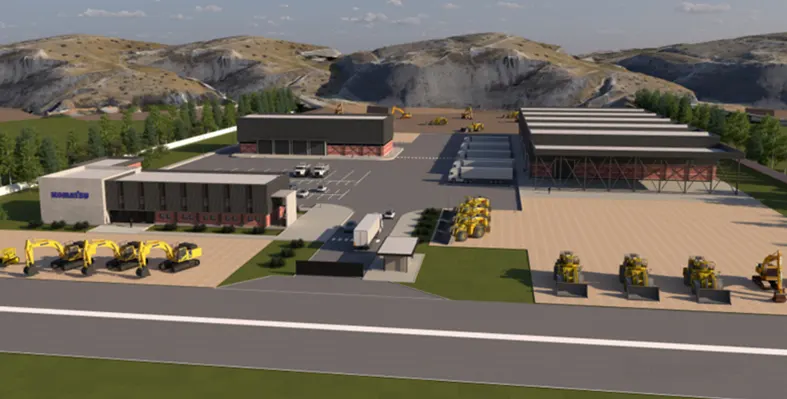
Komatsu to open training center in Côte d’Ivoire, boosting skills for Africa’s construction and mining sectors. (Image source: Komatsu)
Komatsu Ltd., led by President and CEO Takuya Imayoshi, will participate in the 9th Tokyo International Conference on African Development (TICAD 9), scheduled from August 20 to 22 at the Pacifico Yokohama Exhibition Hall
Under the theme “Creating value together through Innovation to empower Africa’s Sustainable Future,” Komatsu will showcase initiatives focused on human resource development, advanced technologies, infrastructure contributions, and corporate social responsibility in Africa.
A centerpiece of Komatsu’s exhibit is its plan to establish a new training center in Côte d’Ivoire, slated for completion in 2026. This facility will serve as a hub for training construction equipment operators and mechanics from distributors, customers, and local communities across West Africa. Initially focused on skills development, the center will use Komatsu Group’s advanced simulators to provide practical training aimed at improving operator proficiency and creating job opportunities. Over time, Komatsu intends to expand the facility’s functions to include equipment stock, parts depot, and marketing capabilities, positioning it as the company’s core facility in West Africa.
To support this goal, Komatsu will demonstrate compact simulators for hydraulic excavators and bulldozers at TICAD 9. These VR-based training tools enable safe, immersive learning experiences and are planned for use at the new training center.
Additionally, Komatsu will display its latest hydraulic excavator model, the PC200i-12, featuring advanced 3D construction capabilities. This equipment enhances operational efficiency and precision, even for less experienced operators, and supports the development of quality infrastructure—an essential element for Africa’s continued growth.
Komatsu has been active in Africa since the 1960s, gradually expanding its footprint by opening offices and distributorships, including a presence in South Africa. With Africa’s rising demand for construction and mining equipment driven by population growth and abundant natural resources, the need for skilled operators and vocational training remains critical.
Currently, Komatsu operates 22 training centers across 15 countries, including facilities in South Africa, Dubai, and Japan. The company is committed to leveraging its expertise in human resource development to address social challenges and support sustainable growth in Africa. Through its initiatives and investments, Komatsu aims to empower the continent’s future by building local talent and strengthening its regional presence.
Infrastructure growth lifts forklift demand
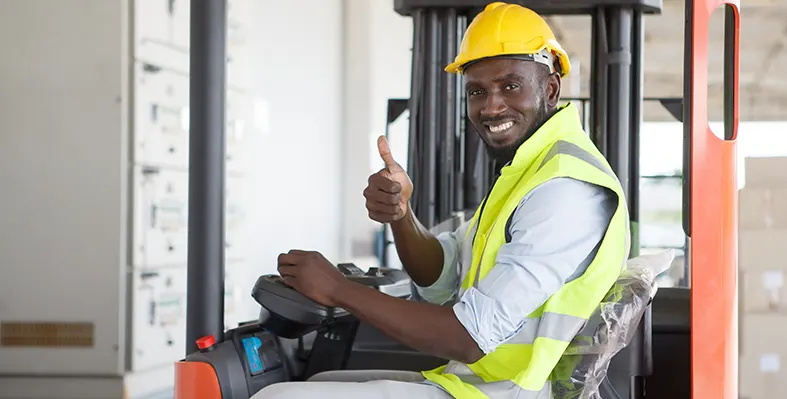
Chinese forklift makers shift focus to Africa as infrastructure growth fuels regional demand and localisation efforts
Chinese manufacturers are keen to localise production in Africa to reduce costs as the market for forklift trucks expands on the back of an infrastructure boom
Infrastructure projects are poised to drive demand for forklifts across Africa by around 4-5% per annum over the next five years, new research suggests. Forklift shipments to the African market in 2024 reached 21,082 units, based on Interact Analysis’ Global Forklift Market report.
Driving demand, it noted, was a surge in new infrastructure projects, particularly in North Africa as well as the Middle East. The research cited Egypt and Saudi Arabia as two thriving markets, though Morocco too is experiencing an infrastructure bonanza as it gears up for the 2030 FIFA World Cup.
Maya Xiao, research manager at Interact Analysis, says the global forklift market is experiencing notable shifts in 2025, influenced by varying regional growth patterns, ongoing changes in electrification adoption and the implementation of US tariff policies.
The continued international expansion efforts of Chinese companies is also notable, Xiao adds. Chinese vendors appear to have accelerated localised production capacity to get closer to markets and for improved cost efficiencies. The report cites cost reductions of around 15%. With China’s own massive domestic forklift market of around 800,000 units annually now firmly in a replacement-driven plateau phase, Africa also presents a dynamic growth opportunity.
China targets African market
Chinese manufacturers in particular are shifting their global focus and reducing reliance on direct investment in the US market, which is affected by tariffs, while increasing investment into other regions, including Europe and southeast Asia. This increased investment involves establishing localised manufacturing, enhancing service capabilities and acquiring technology.
Read the complete story in out latest issue here