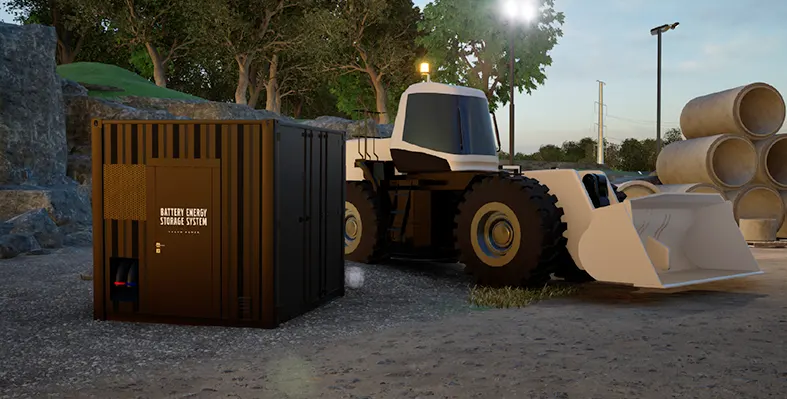
An illustration of an electric application supported by a BESS powered by Volvo Penta’s subsystem. (Image source: Volva Penta)
With emissions regulations tightening and electricity demand exceeding grid capacity, the construction and mining sectors are facing a growing need for energy storage solutions. To address these challenges, Volvo Penta has introduced a compact and energy-dense Battery Energy Storage System (BESS) subsystem
Designed for transportability and fast charging, this solution provides system integrators and BESS manufacturers with a reliable option for deploying energy storage in microgrid applications such as quarries, urban restoration sites, and other demanding environments.
A scalable energy storage solution
Construction and mining sites face diverse energy challenges. While some locations have grid access, they require peak shaving or fast-charging solutions to optimise power use. Others must find alternative power sources due to grid constraints, particularly when energy needs are not factored in from the outset. Additionally, projects in transitional phases may find themselves neither fully off-grid nor securely connected to a stable energy supply. Volvo Penta’s BESS subsystem is designed to meet these challenges, supporting industries where energy demands exceed grid capabilities or connectivity is limited. These storage systems integrate seamlessly with renewables and other power sources, ensuring a stable and reliable energy supply essential for electrification in large-scale or remote operations.
Optimised for battery-electric vehicle (BEV) charging, Volvo Penta’s BESS subsystem offers a high C-rate, ensuring fast charging while maintaining grid stability in high-demand environments. As industries continue their shift toward electrification, the system provides a crucial solution to mitigate capacity and frequency fluctuations, ensuring consistent energy availability.
Beyond BEV charging, the BESS subsystem supports microgrid applications and peak shaving strategies. Its transportable design enables flexible deployment in zero-emission construction zones and remote mining sites. The system powers equipment directly on-site and can be relocated for recharging without disrupting operations. Additionally, it enhances the performance of stationary electric equipment, such as excavators, wheel loaders, and crushers, ensuring continuous uptime in rugged environments.
At its core, Volvo Penta’s BESS subsystem features an energy-dense battery pack with a high-performance C-rating for efficient fast charging and discharging. Built on proven battery technology from Volvo Group’s on- and off-highway applications, the system is designed to endure harsh conditions, boasting a high IP rating for corrosion and dust resistance. Additional features include a DC/DC converter for auxiliary power, a telematics gateway for real-time monitoring, and an advanced thermal management system to optimize performance across various environments. The system's CAN and DC interfaces, developed with Volvo Group expertise, ensure secure data transfer, while its robust Battery Management System (BMS) enhances performance, extends battery life, and safeguards cybersecurity.
Each Volvo Penta BESS subsystem delivers essential DC energy supply, while original equipment manufacturers (OEMs) manage AC setup, container integration, and system configuration.This collaborative approach enables tailored energy solutions to meet diverse operational needs.
Following extensive testing and prototyping with customers, Volvo Penta is now bringing its production-ready BESS subsystem to market. The company will showcase these advanced energy storage solutions at bauma 2025. Attendees can visit Volvo Penta’s stand (A4.412) to meet experts and explore how BESS technology can support the transition to electrification in the construction and mining industries.